Atelier
Yek
Design. Photography. Art. Fabrication.
Reuse oak with mold cleaned and used to create a Bench + Chair. Using a jig to set angle and height to construct steel frame piece by piece to fit.
Initially designed as a task arm chair which then evolved into a casual dinning chair only to then be influenced by the found oak reuse to become a hybrid in order to take full advantage of all the character of the wood.
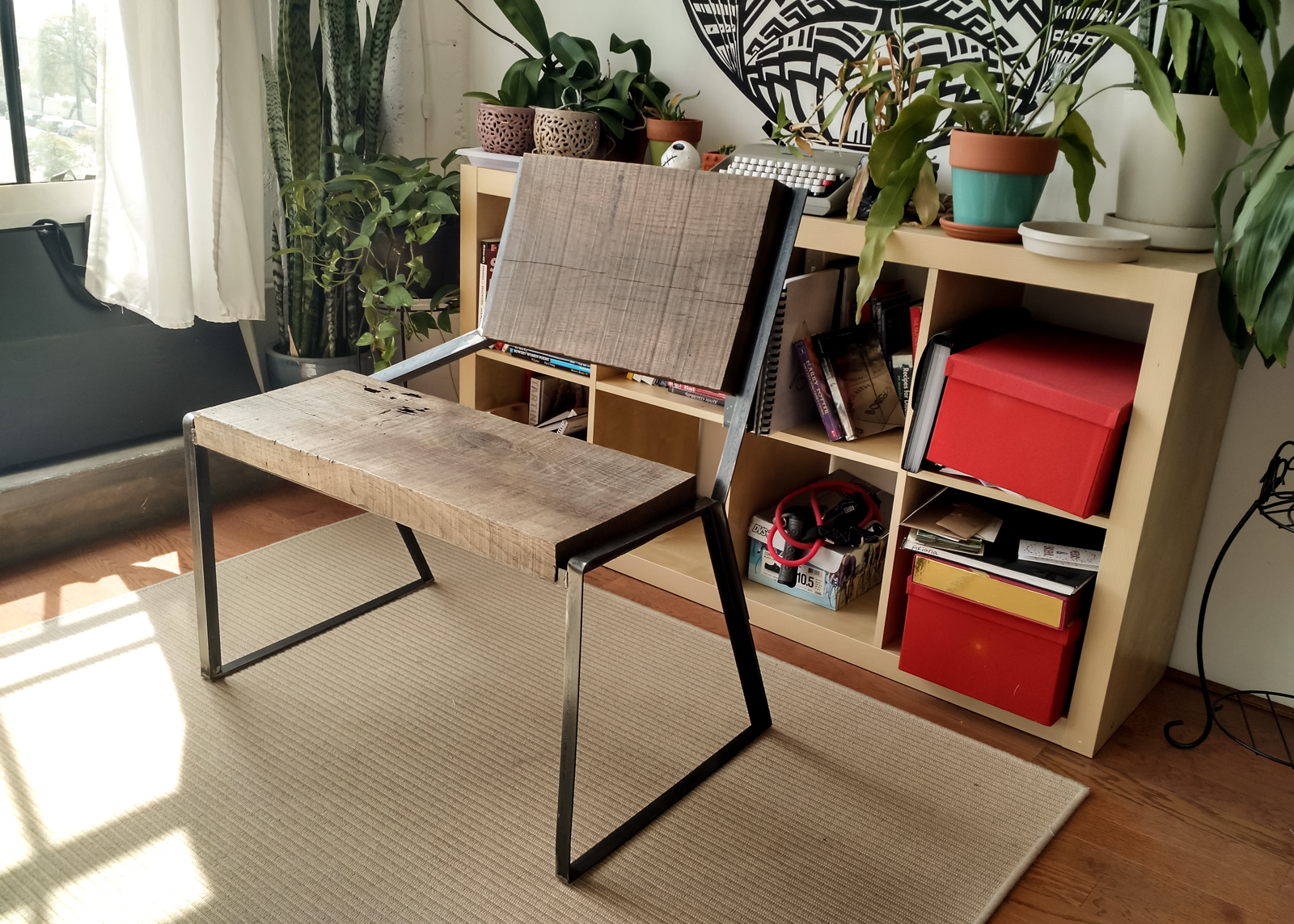

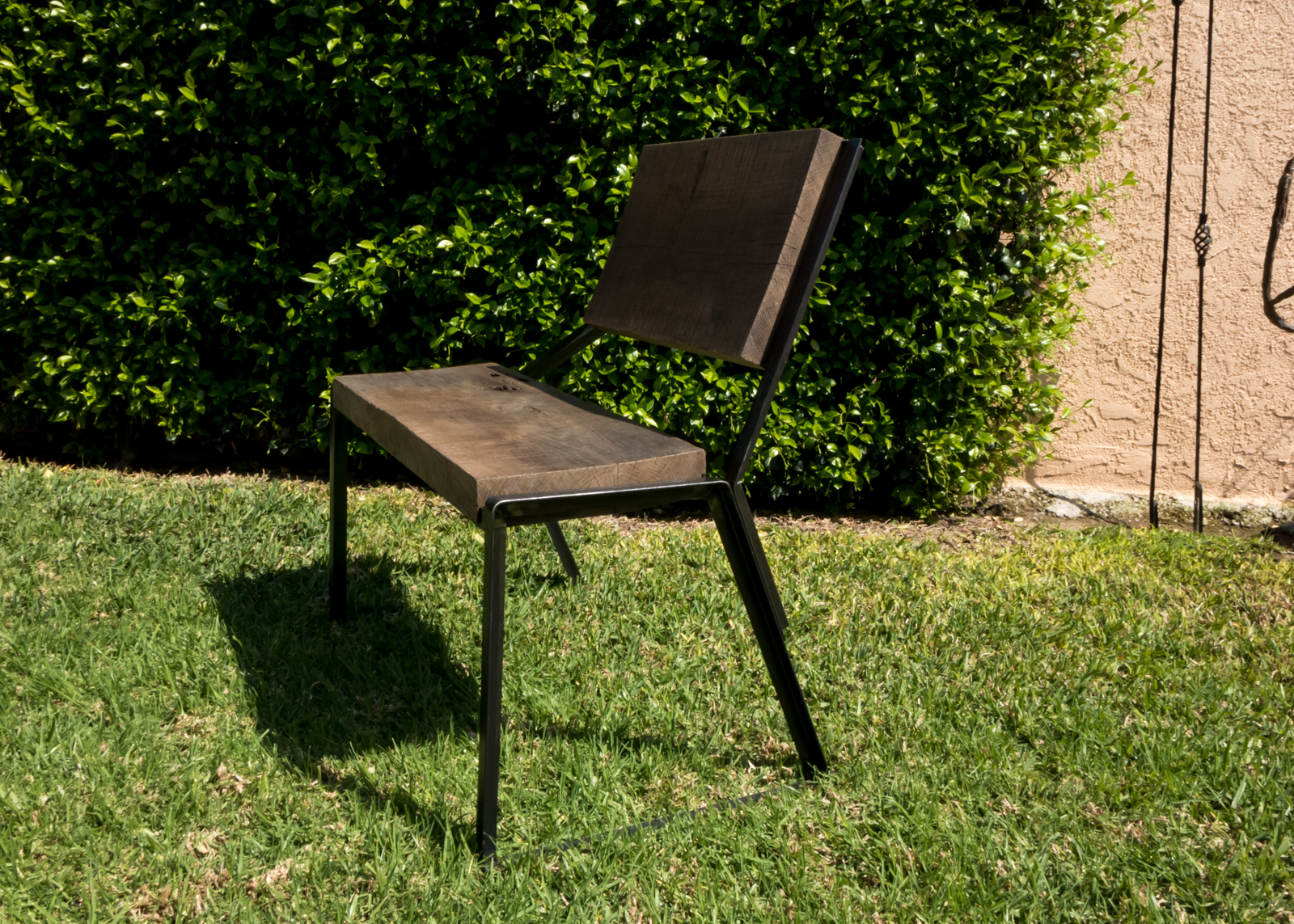


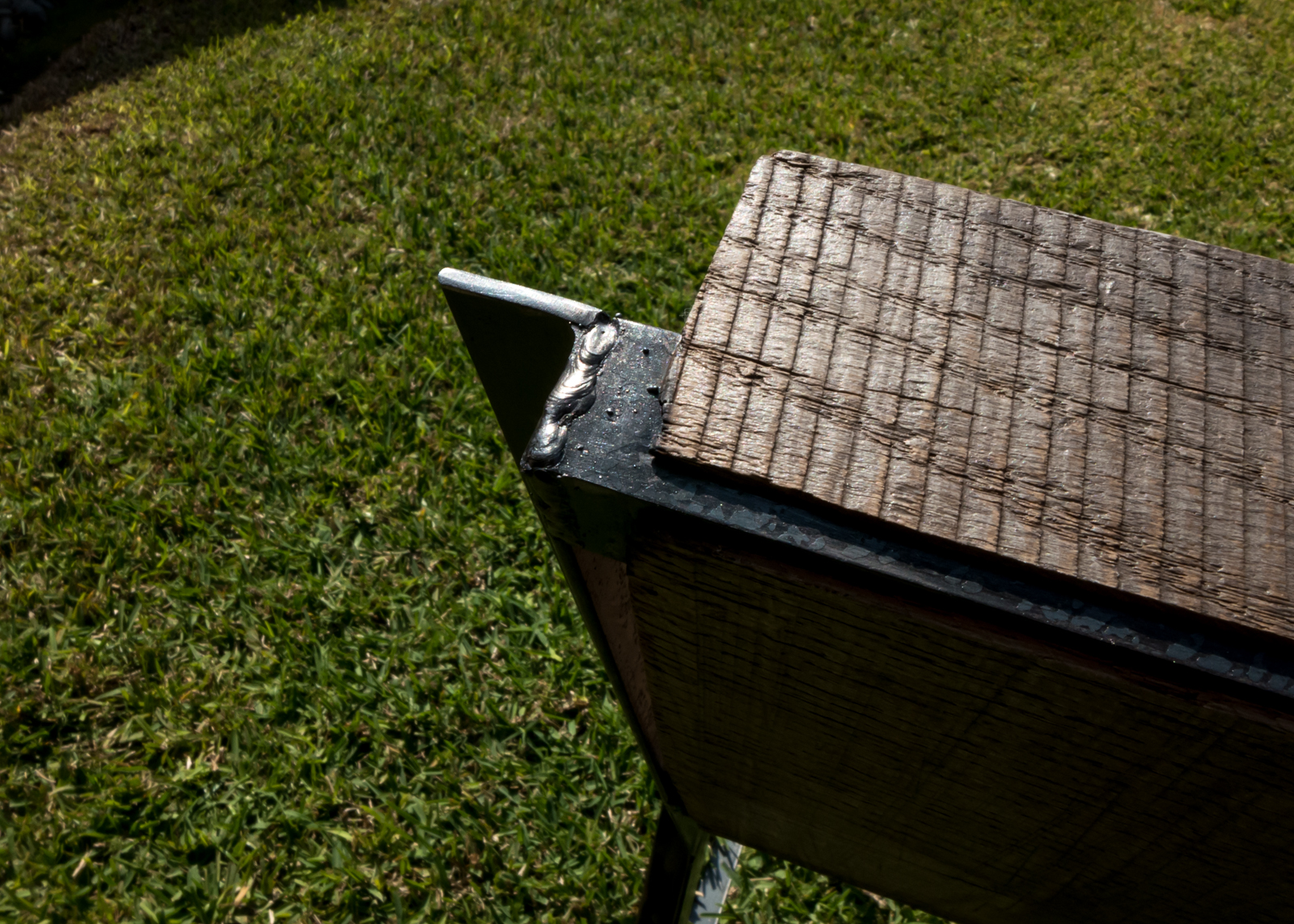

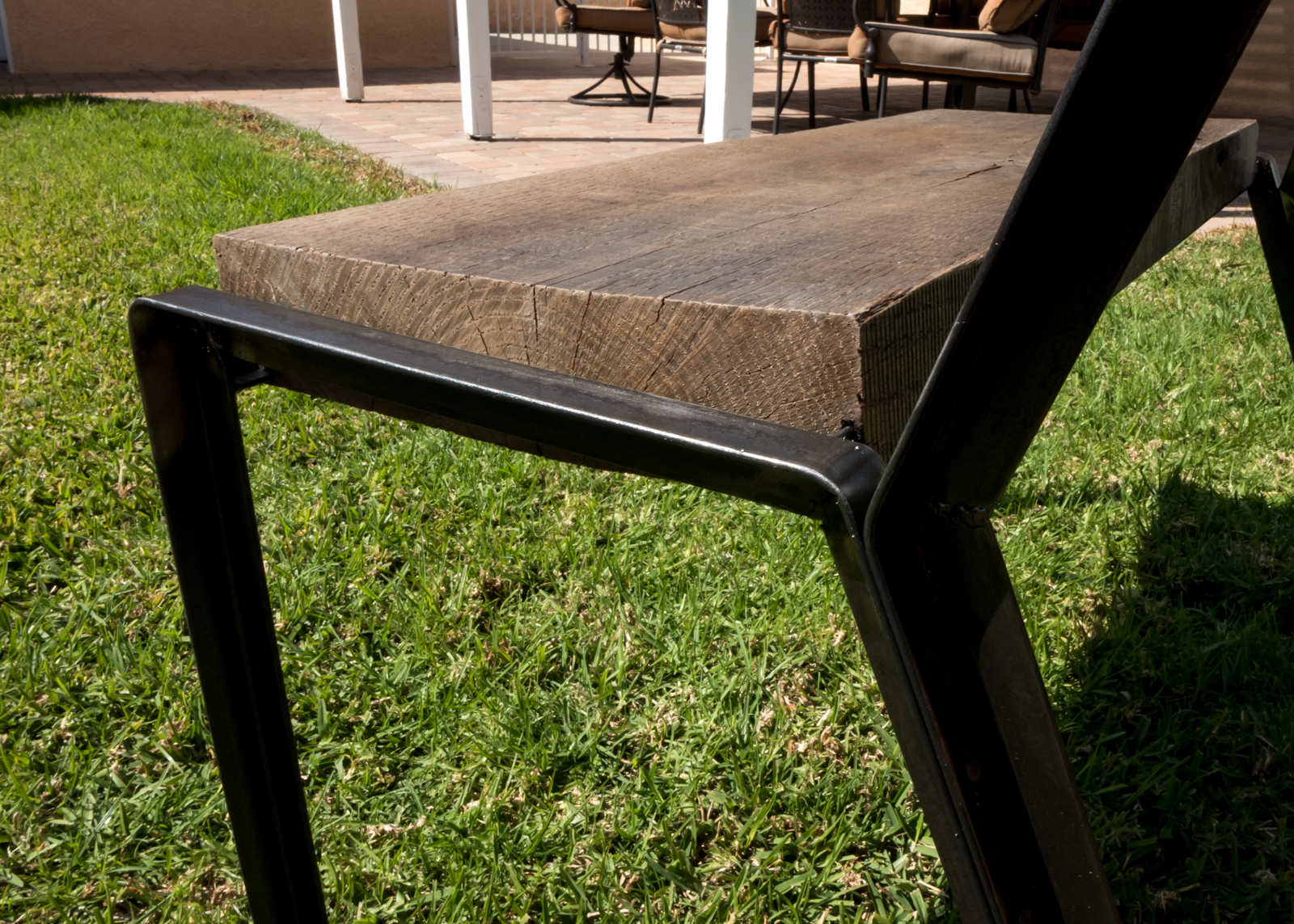
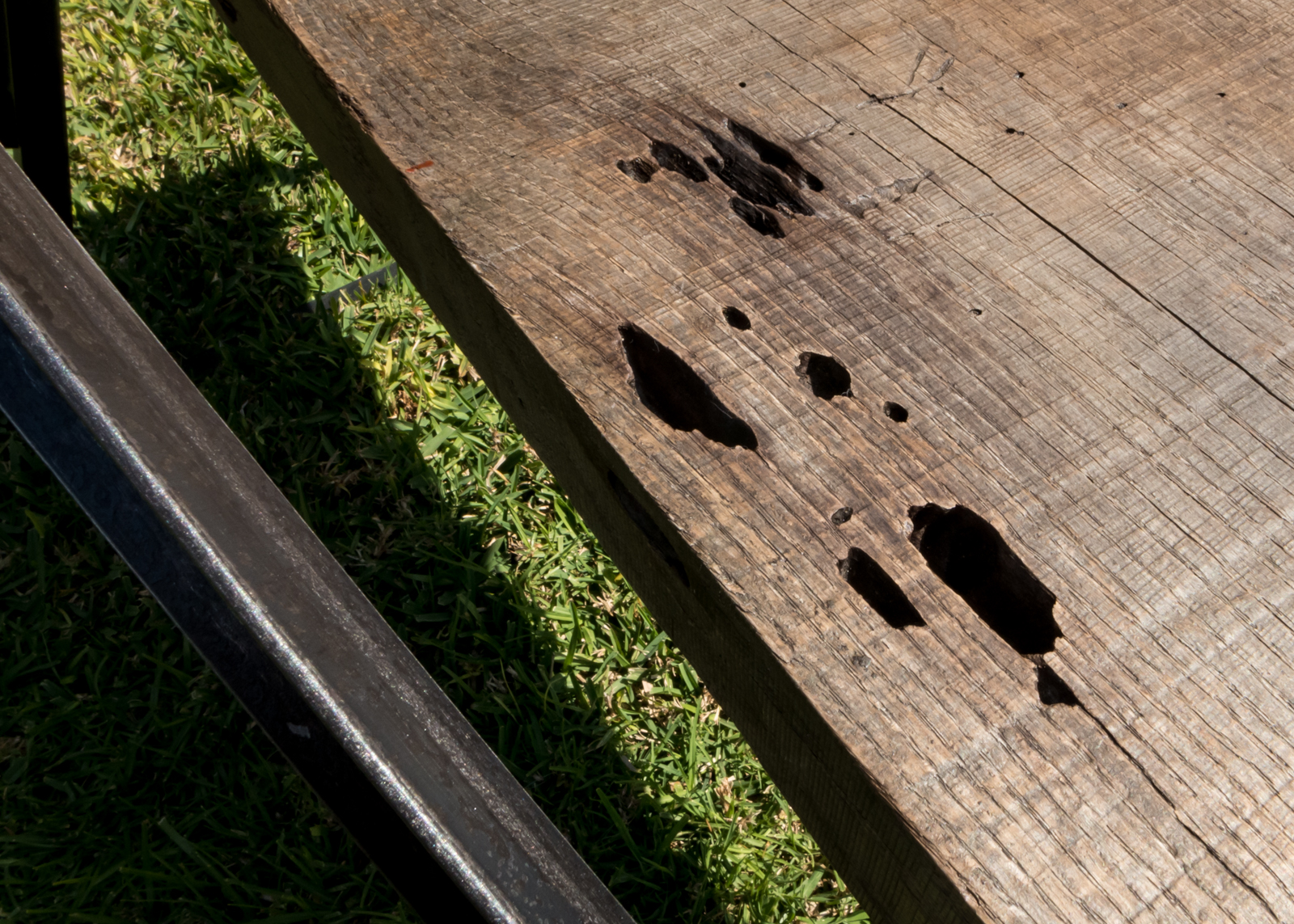
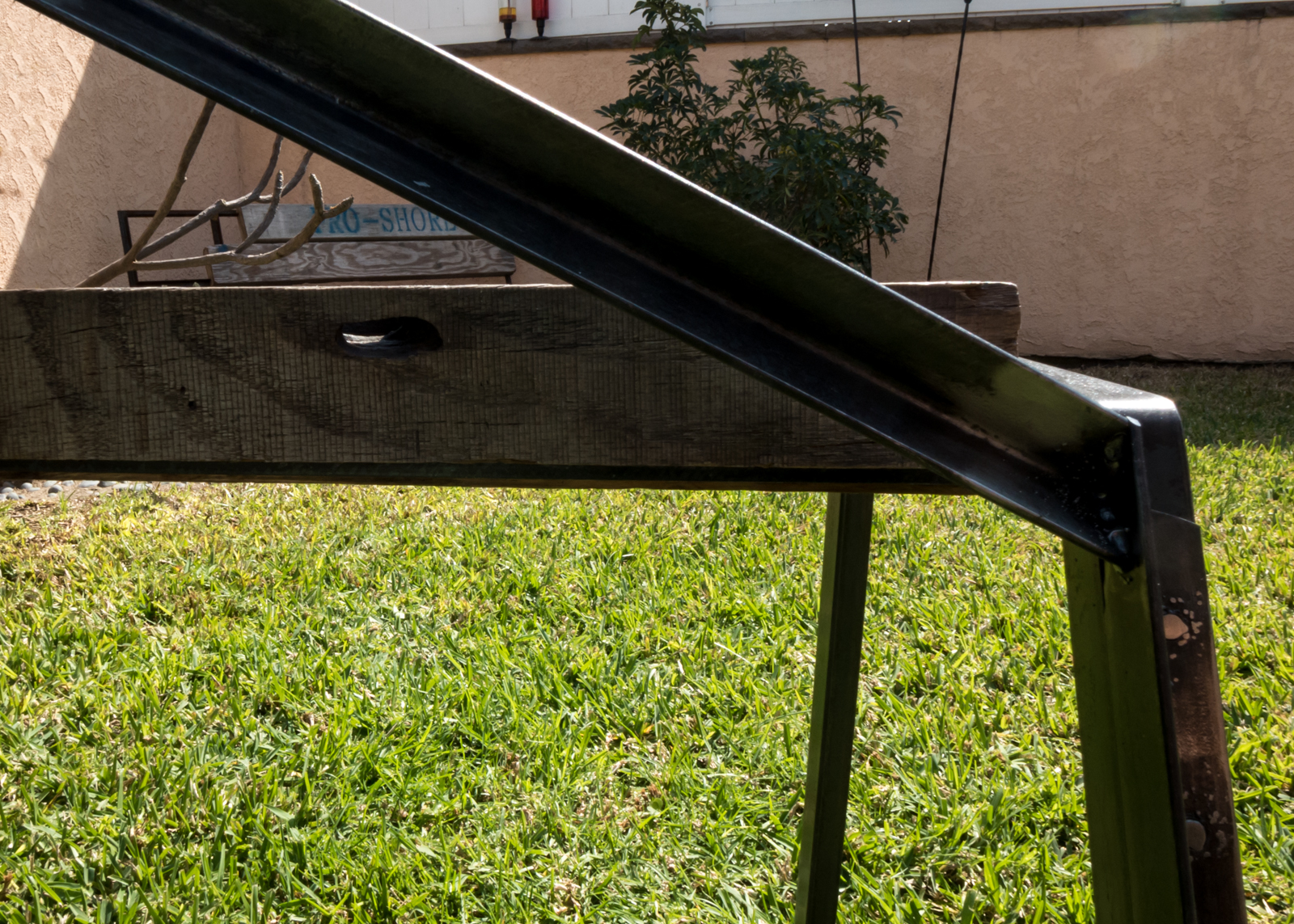
Unlike the few other pieces I initially tried to plan the design of the chair. Starting with sketches and Rhino to rough out proportion, dimensions and formal qualities. Once the basics were established I went through a series of quick ink sketches for the frame until I found something that seemed to work with the lumber I had hand picked.





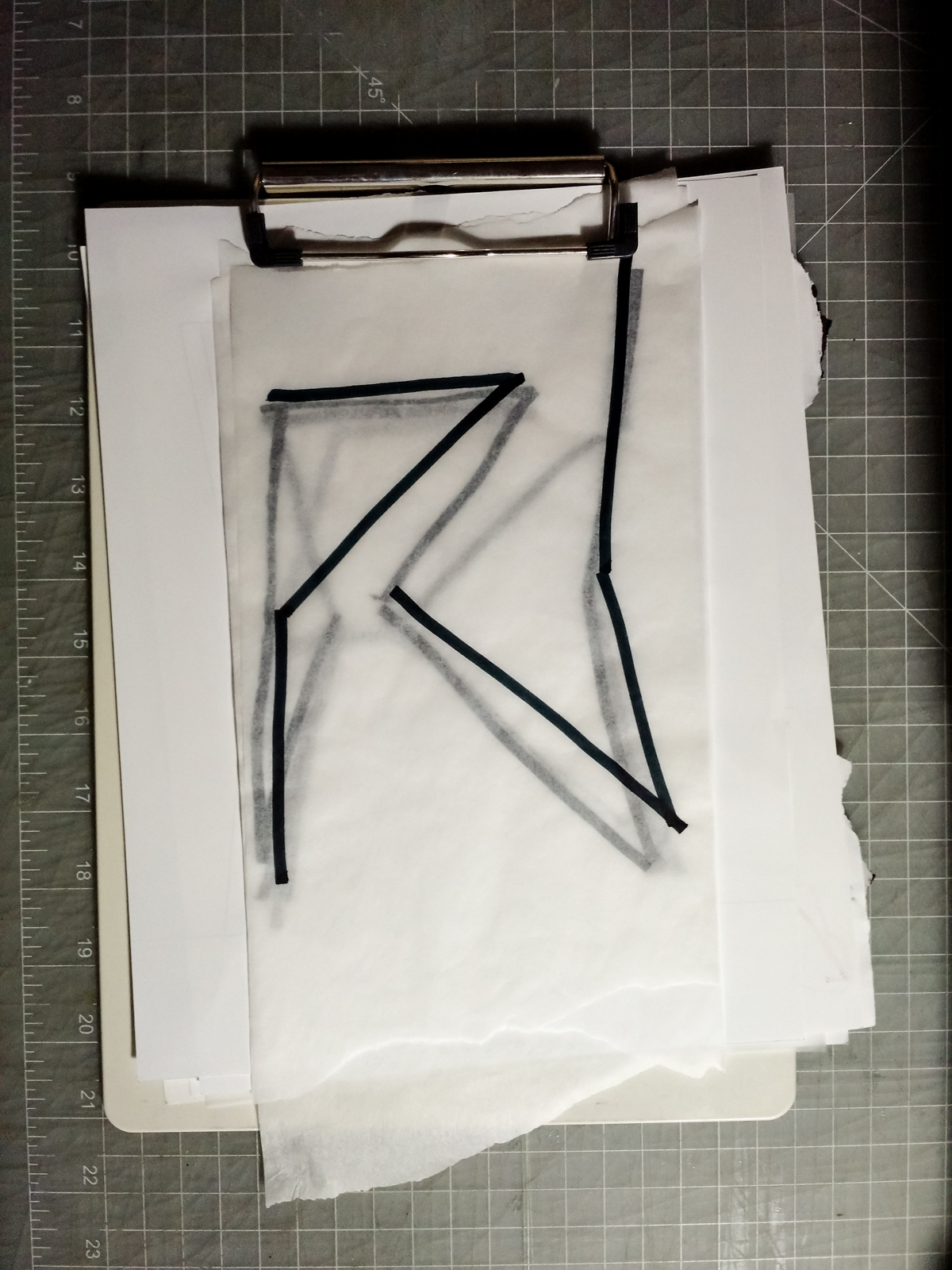

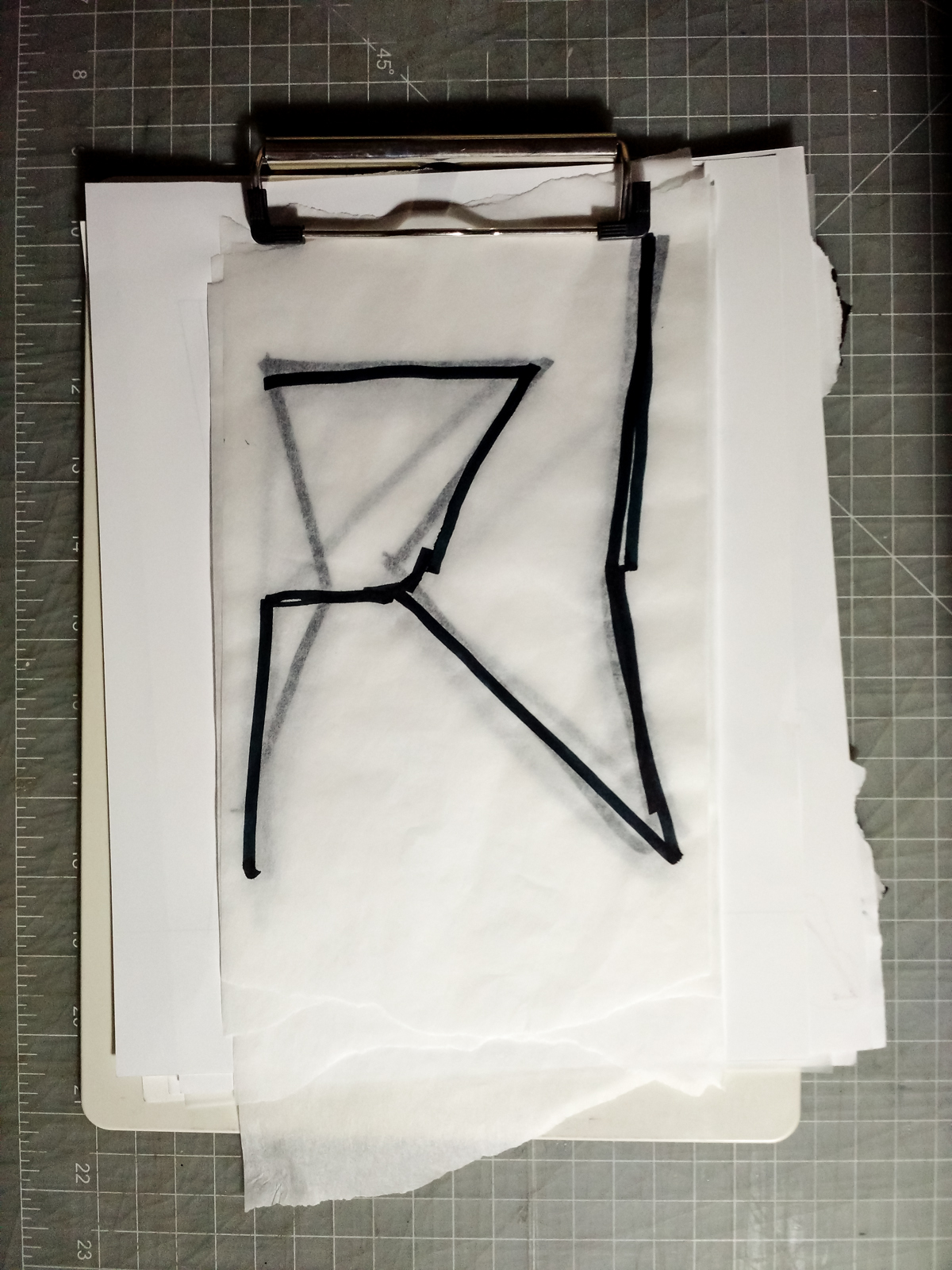


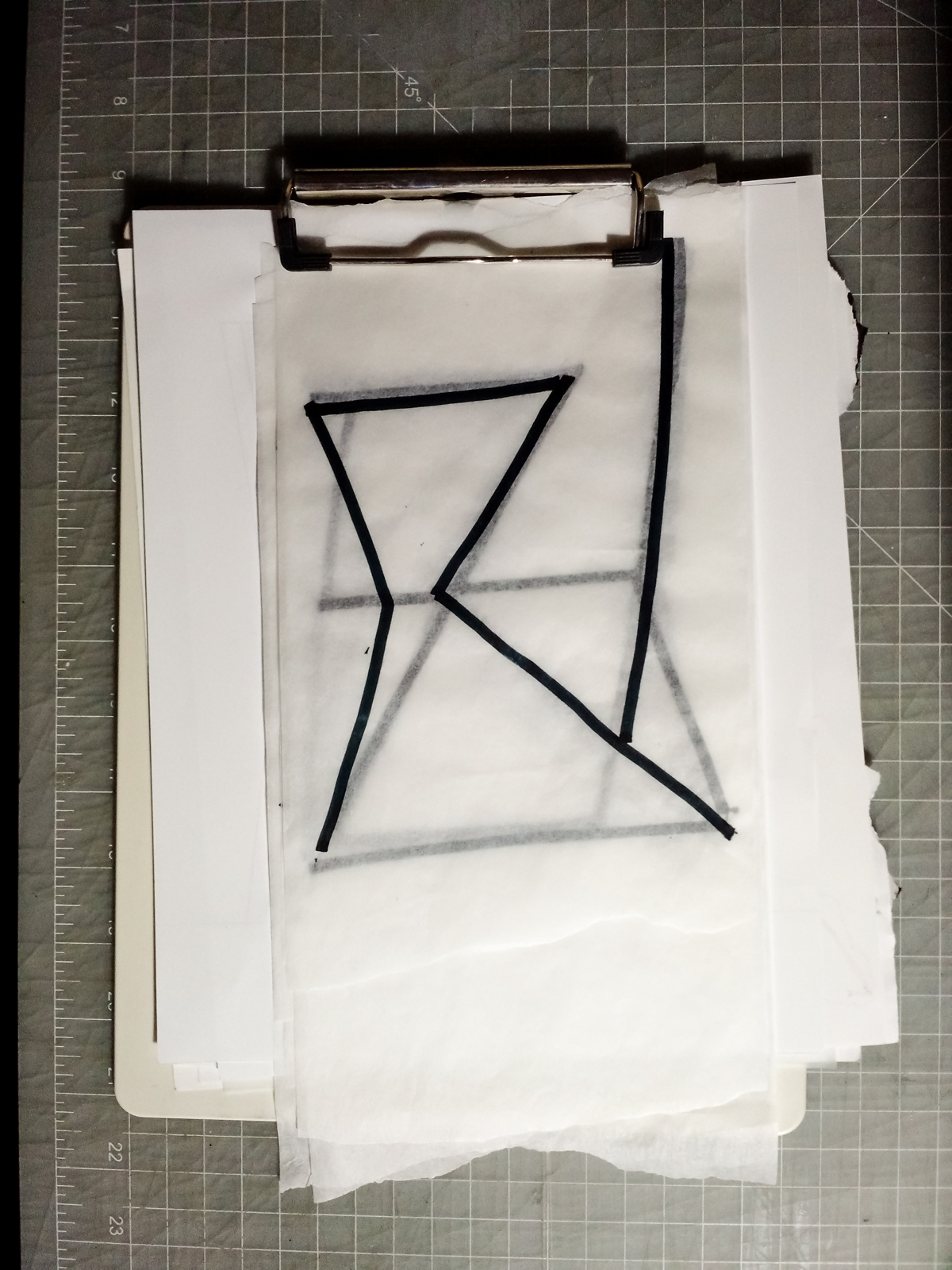


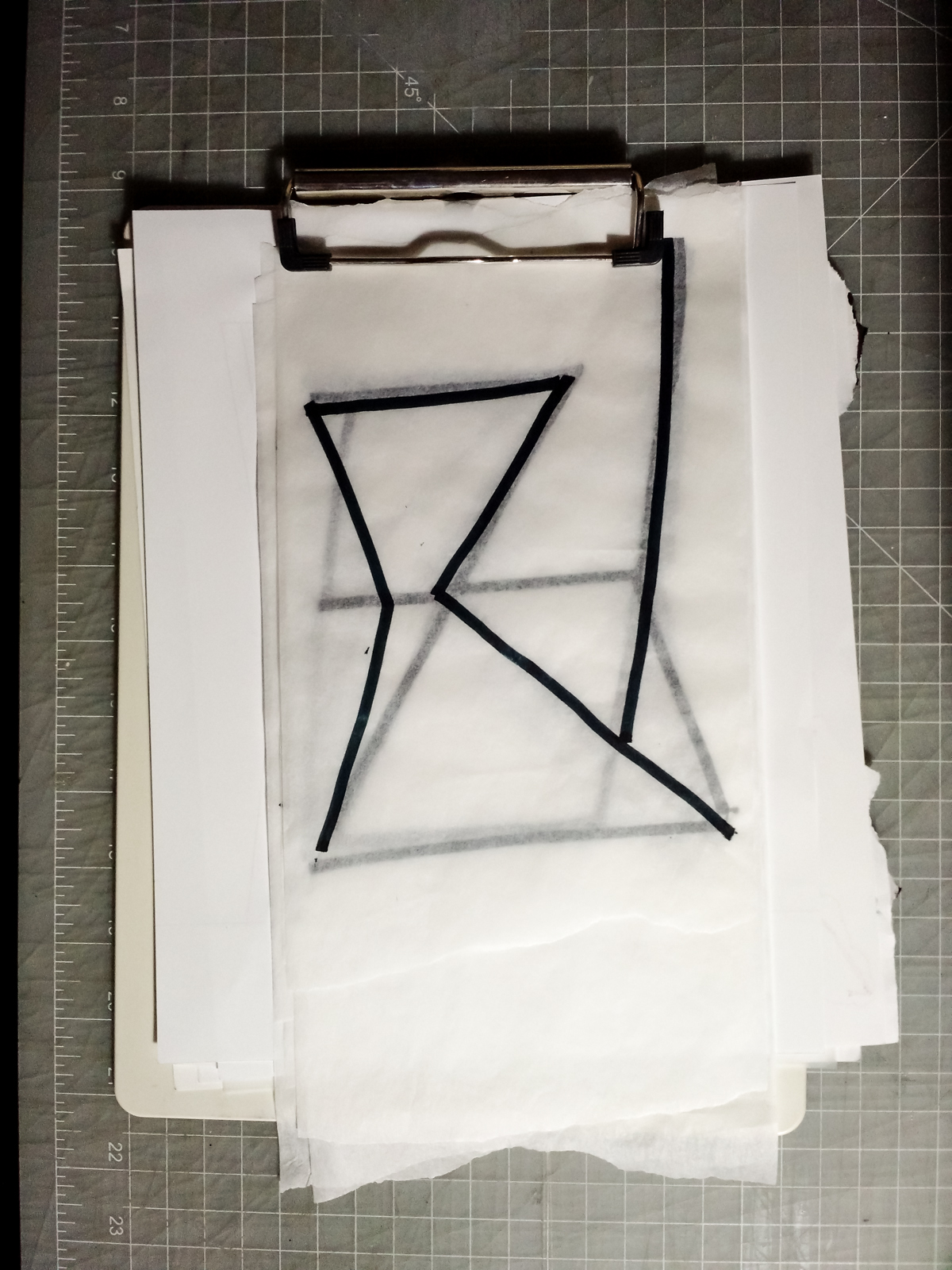



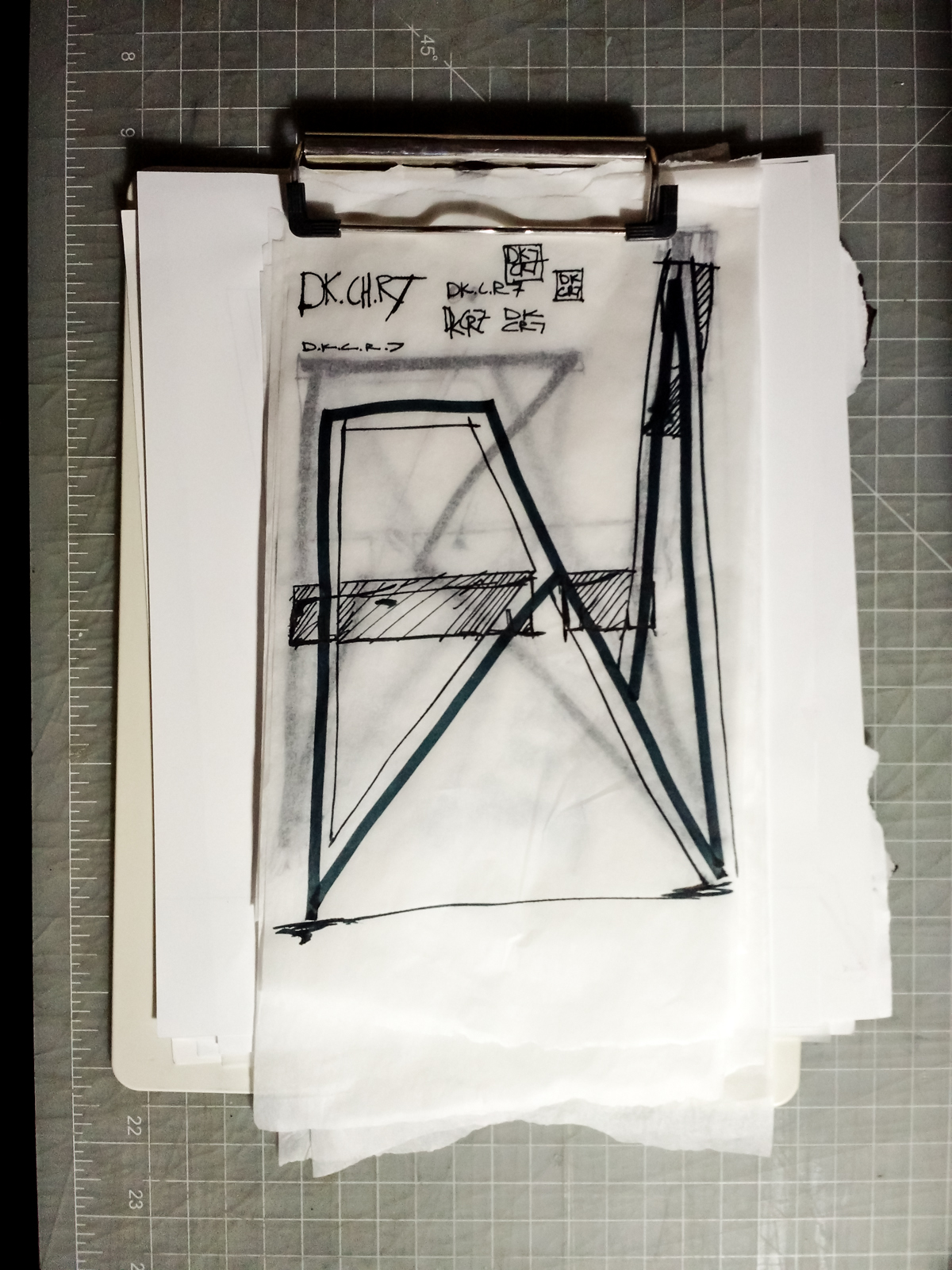

First day of fabrication started with taking a seat and decided what I was to actually do, because I was rather partial to the mold rot I decided not to cut that bit off and leave the seat wider than the back. Once that was decided I started to test out detail ideas particularly the embedded steel angle. Post this it was on to assembling a jig to hold the pieces for the future steel leg fabrication.
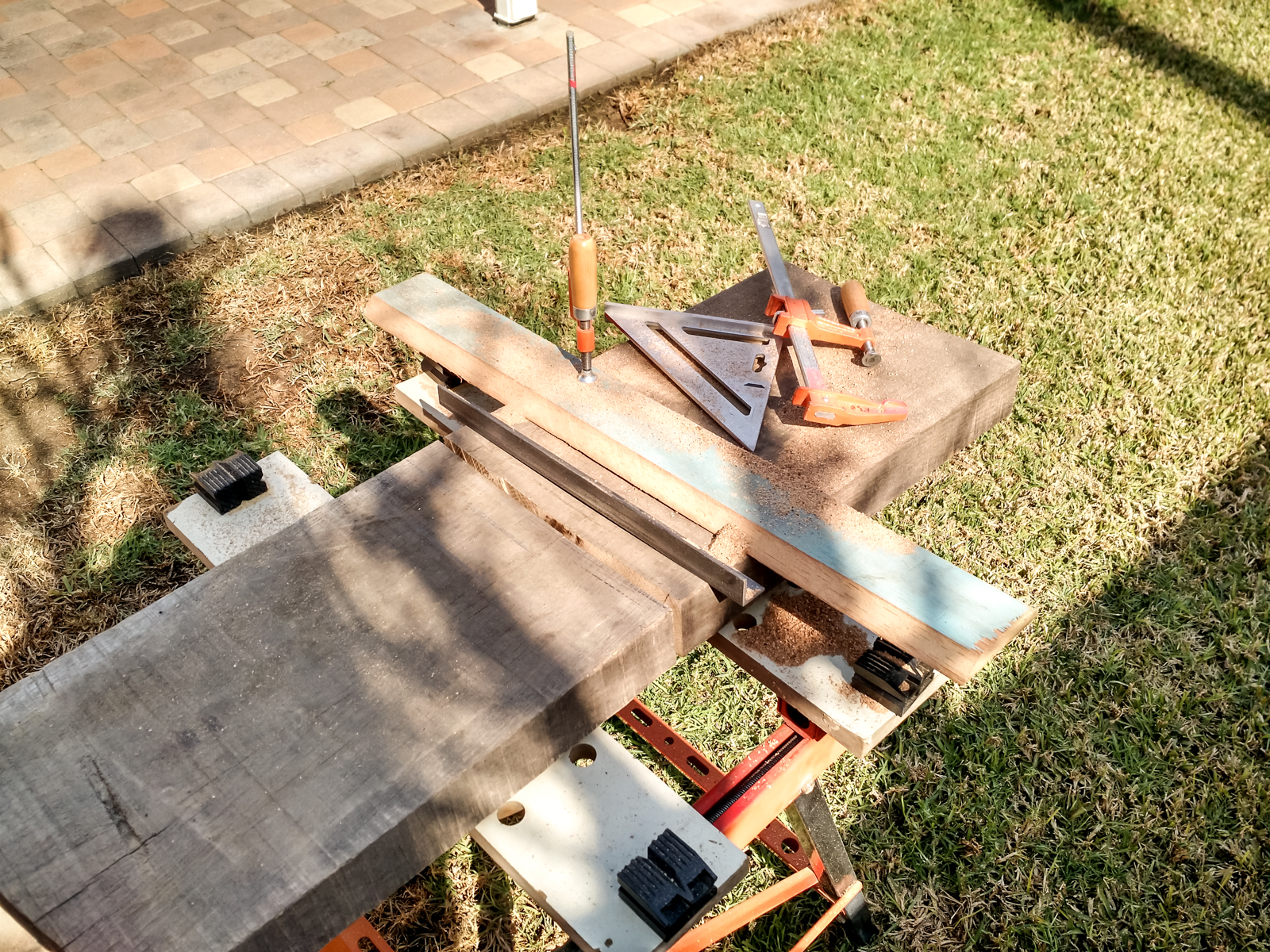
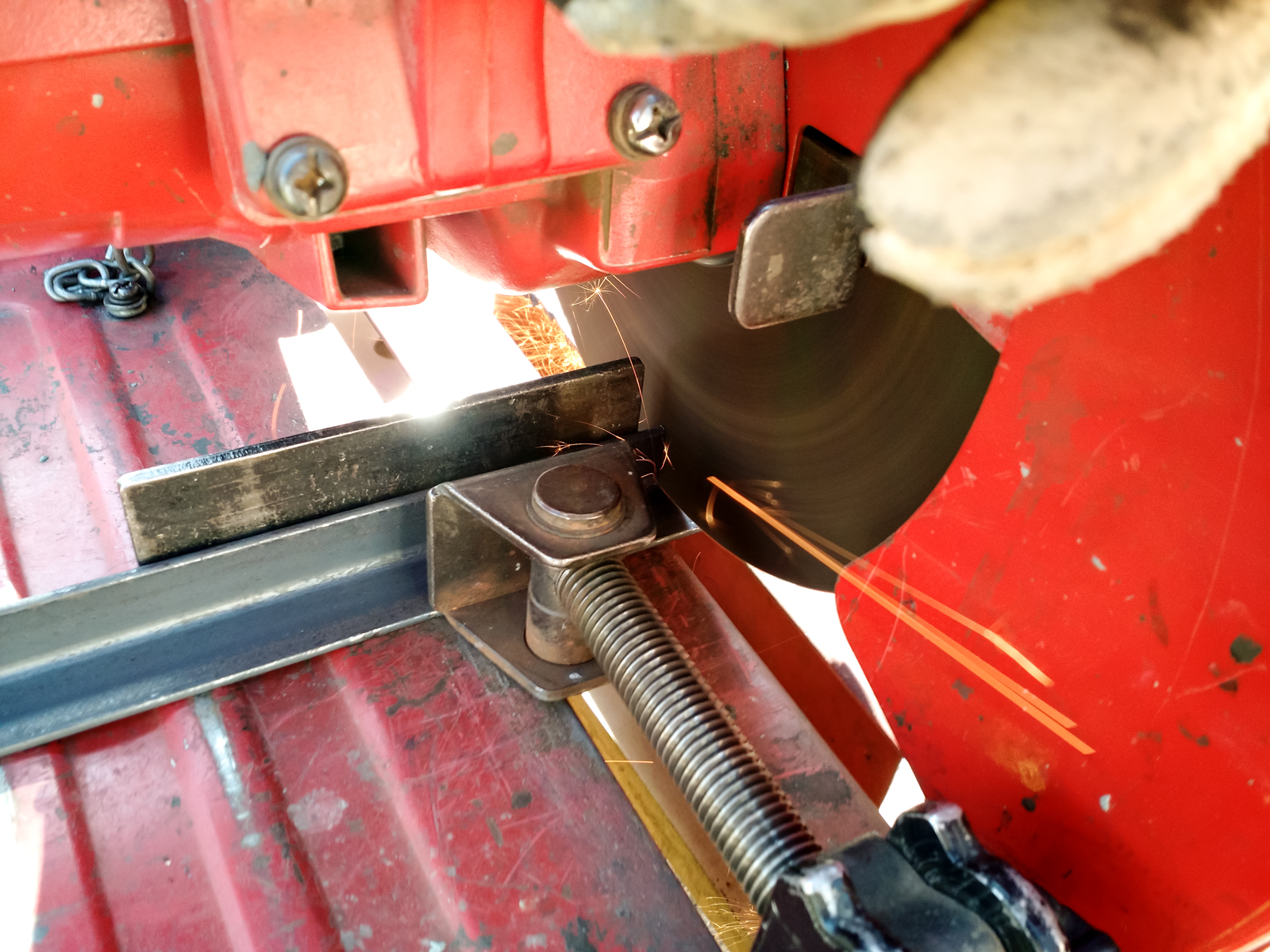


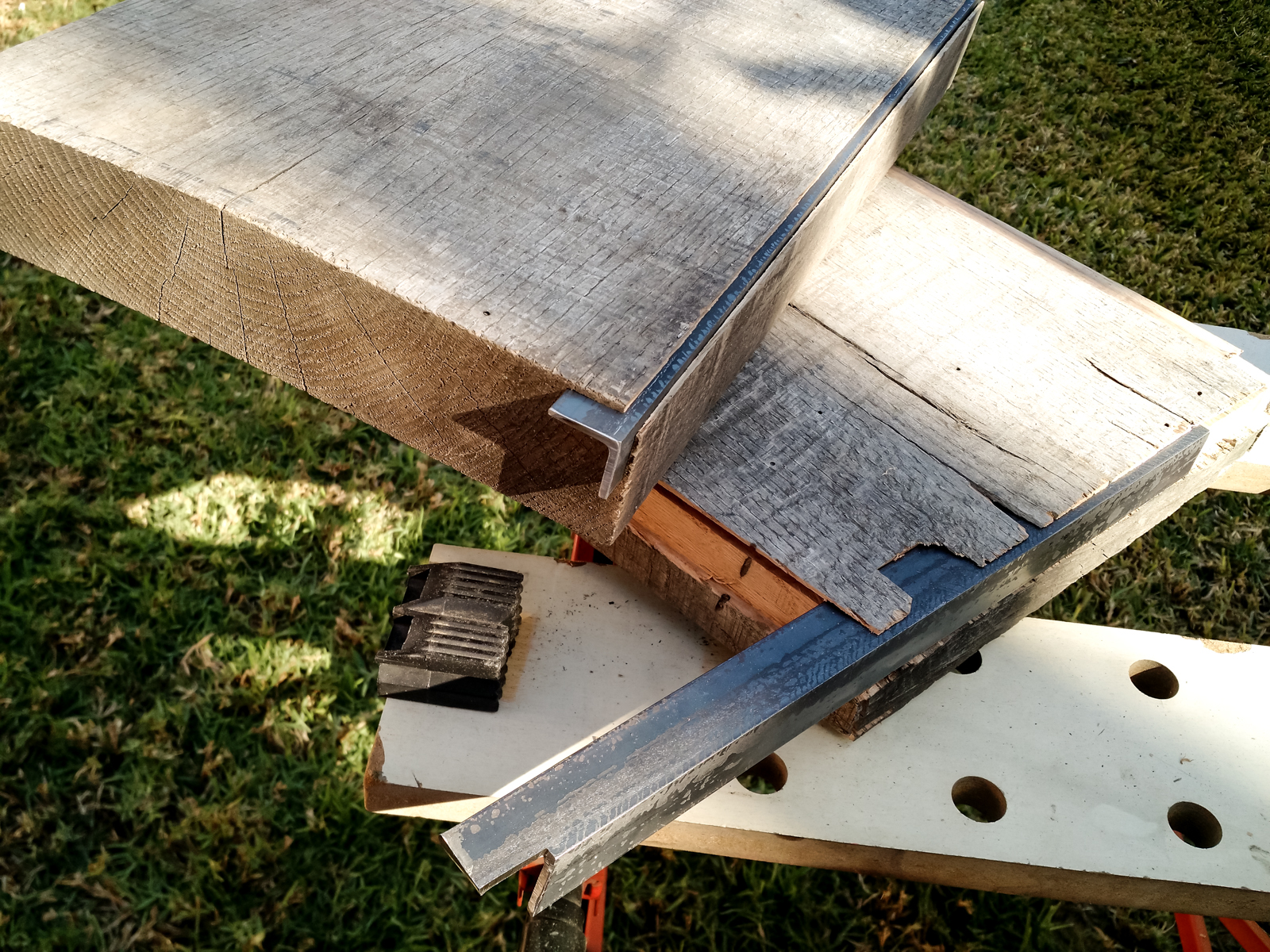
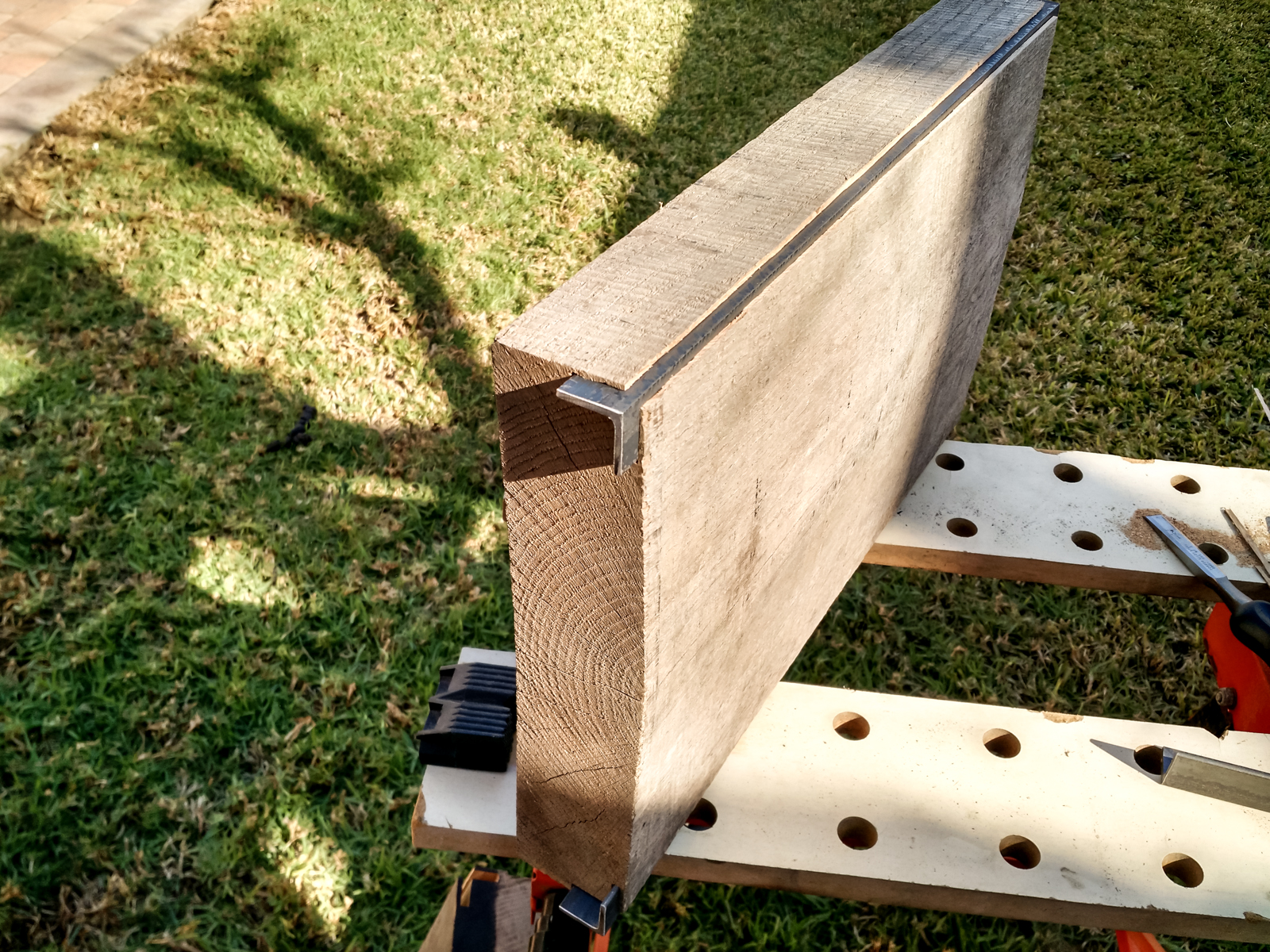
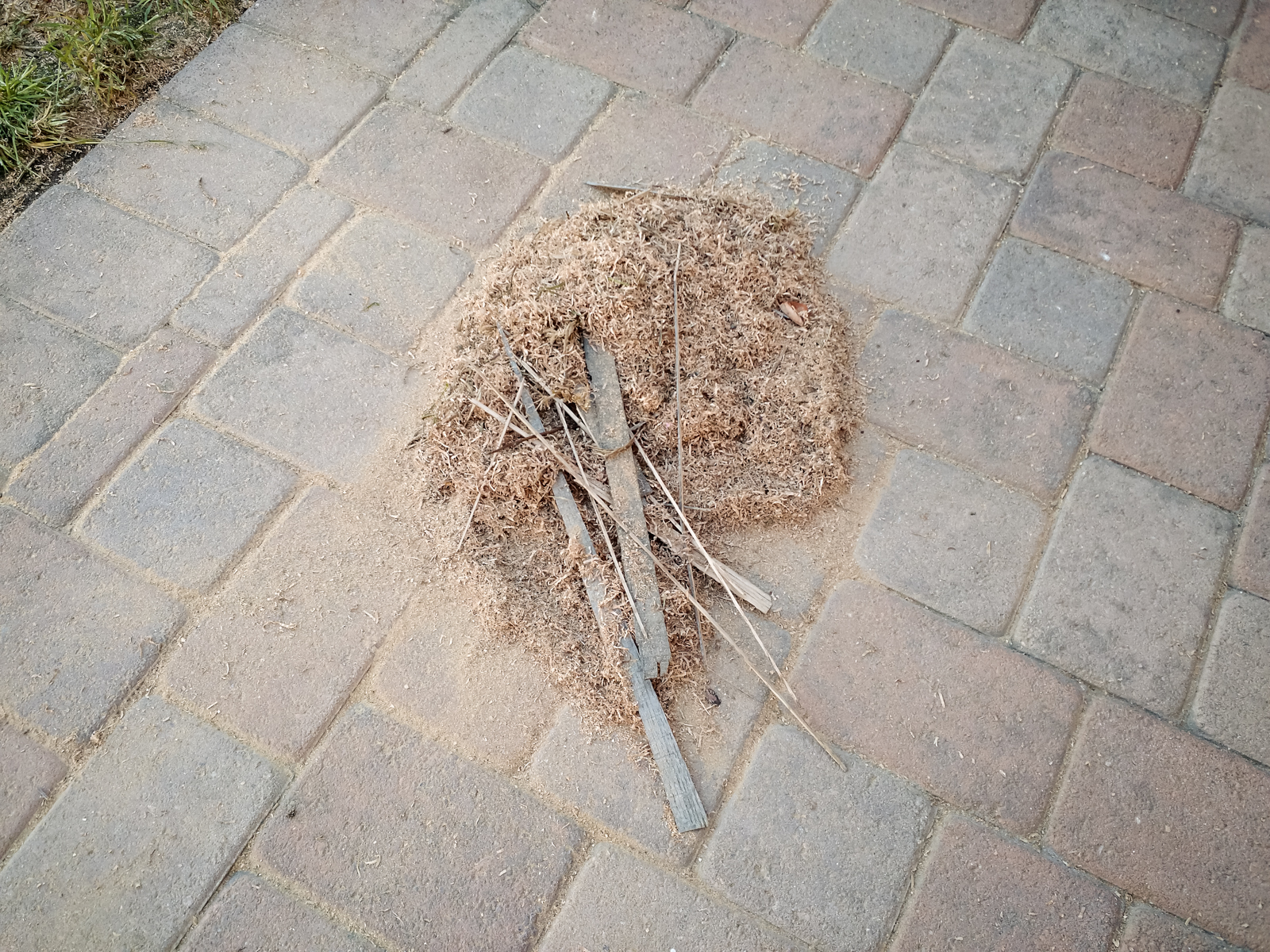

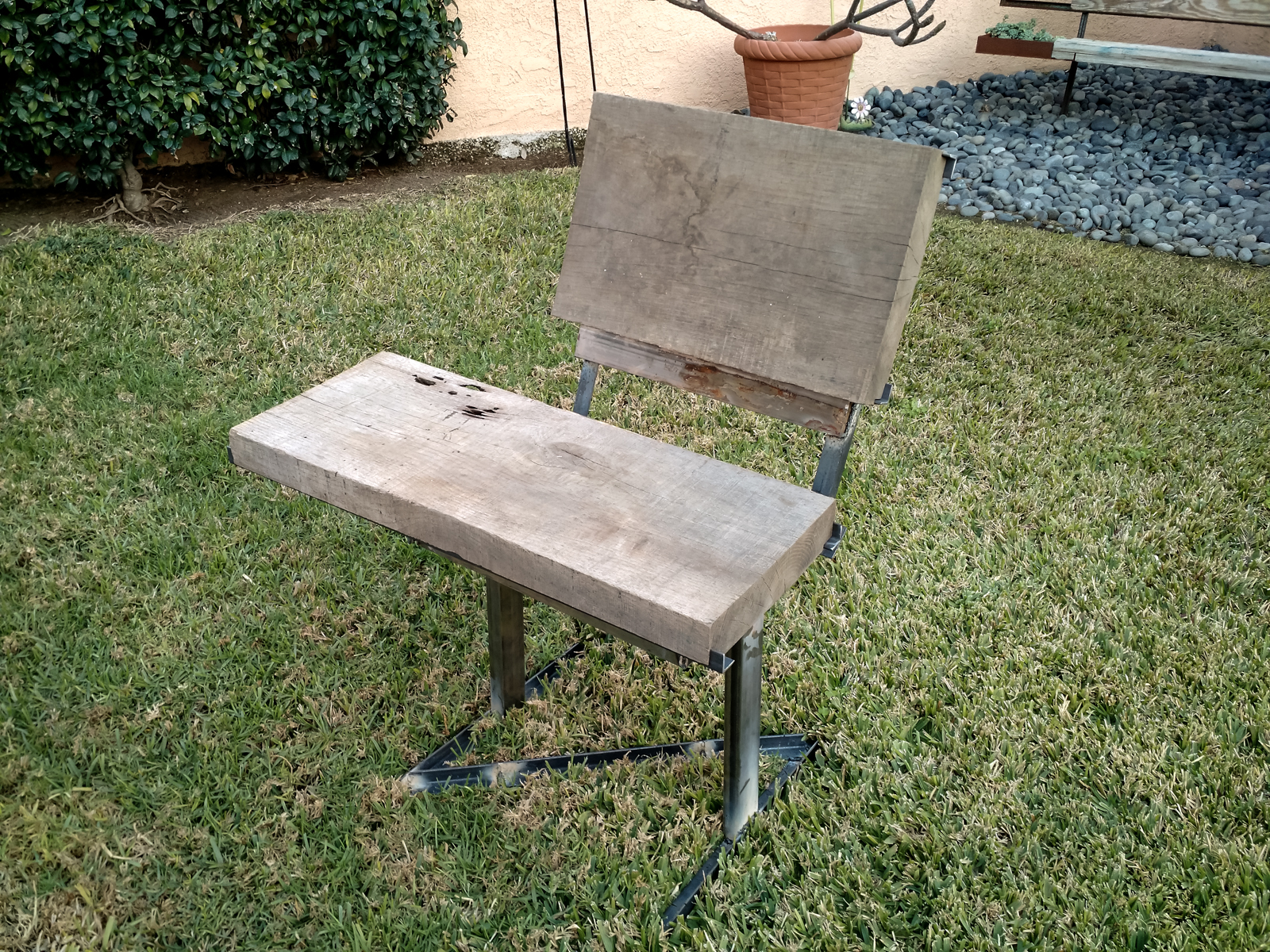



Day two of fabrication began with securing the seat back to the embedded steel angles using piano wire which had to be ground down to size for a snug fit. This would ensure the wood from breaking away from the steel angles. next was mocking up the legs and establishing the technique to cut and bend the steel.


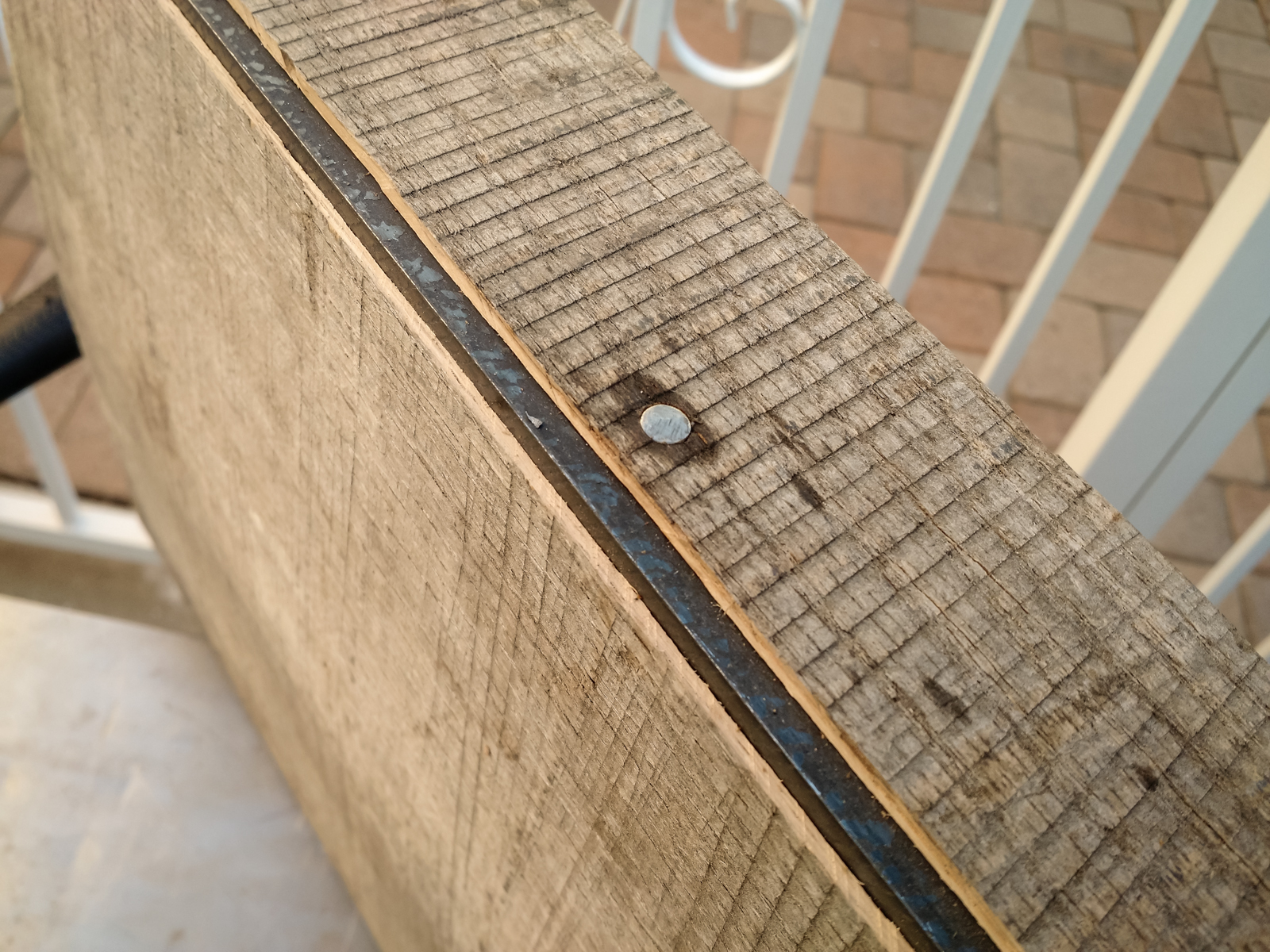
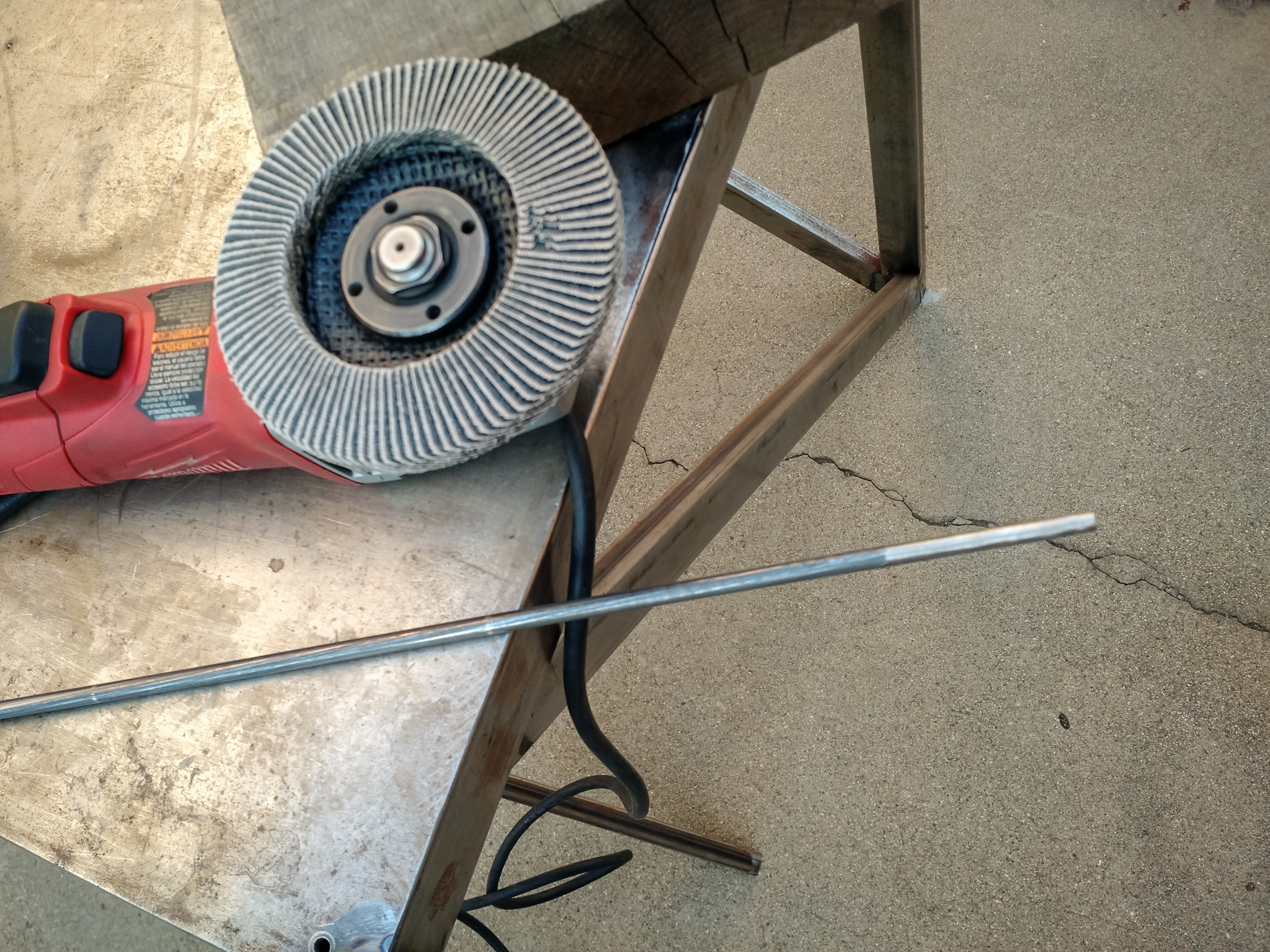



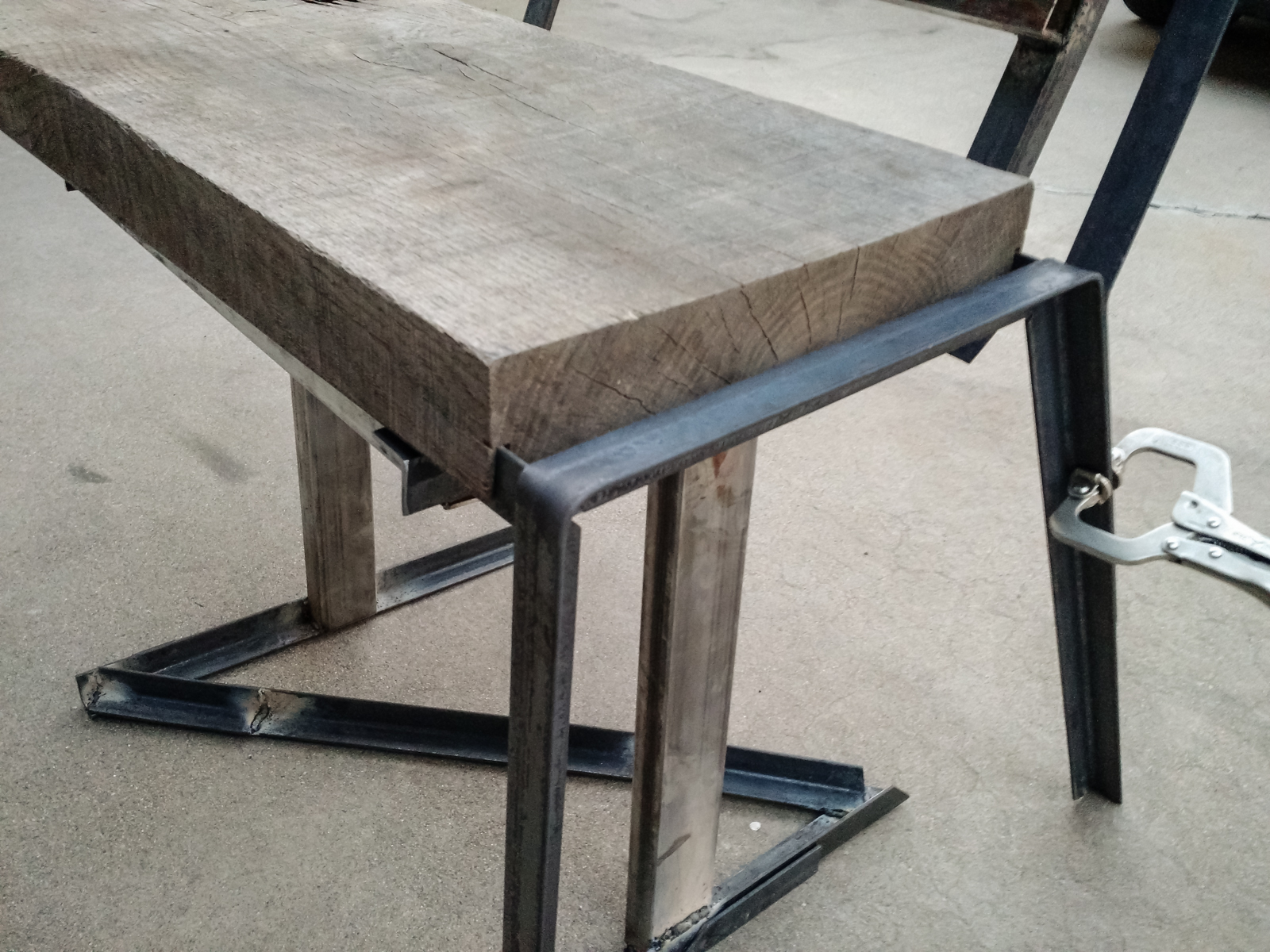
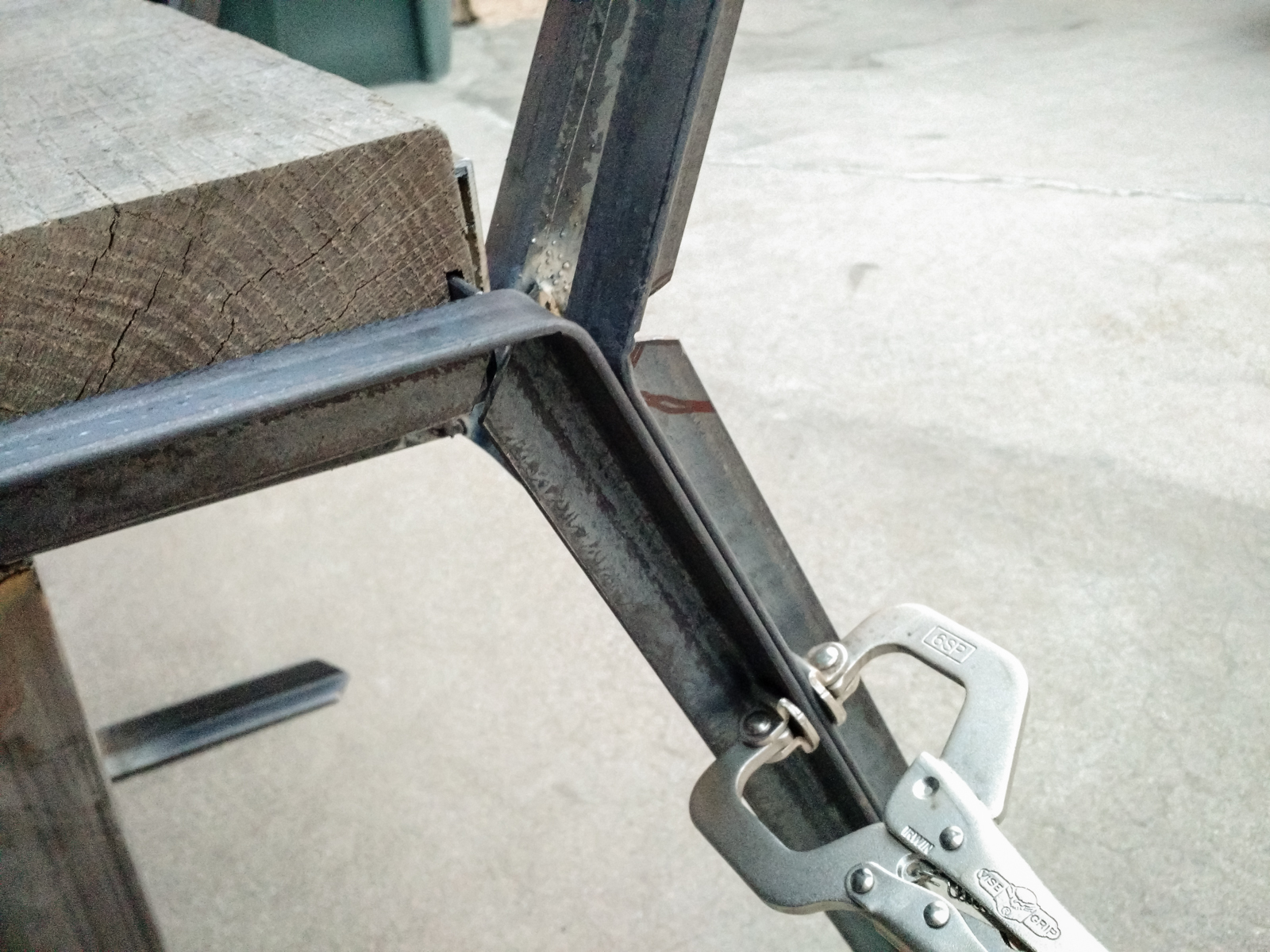


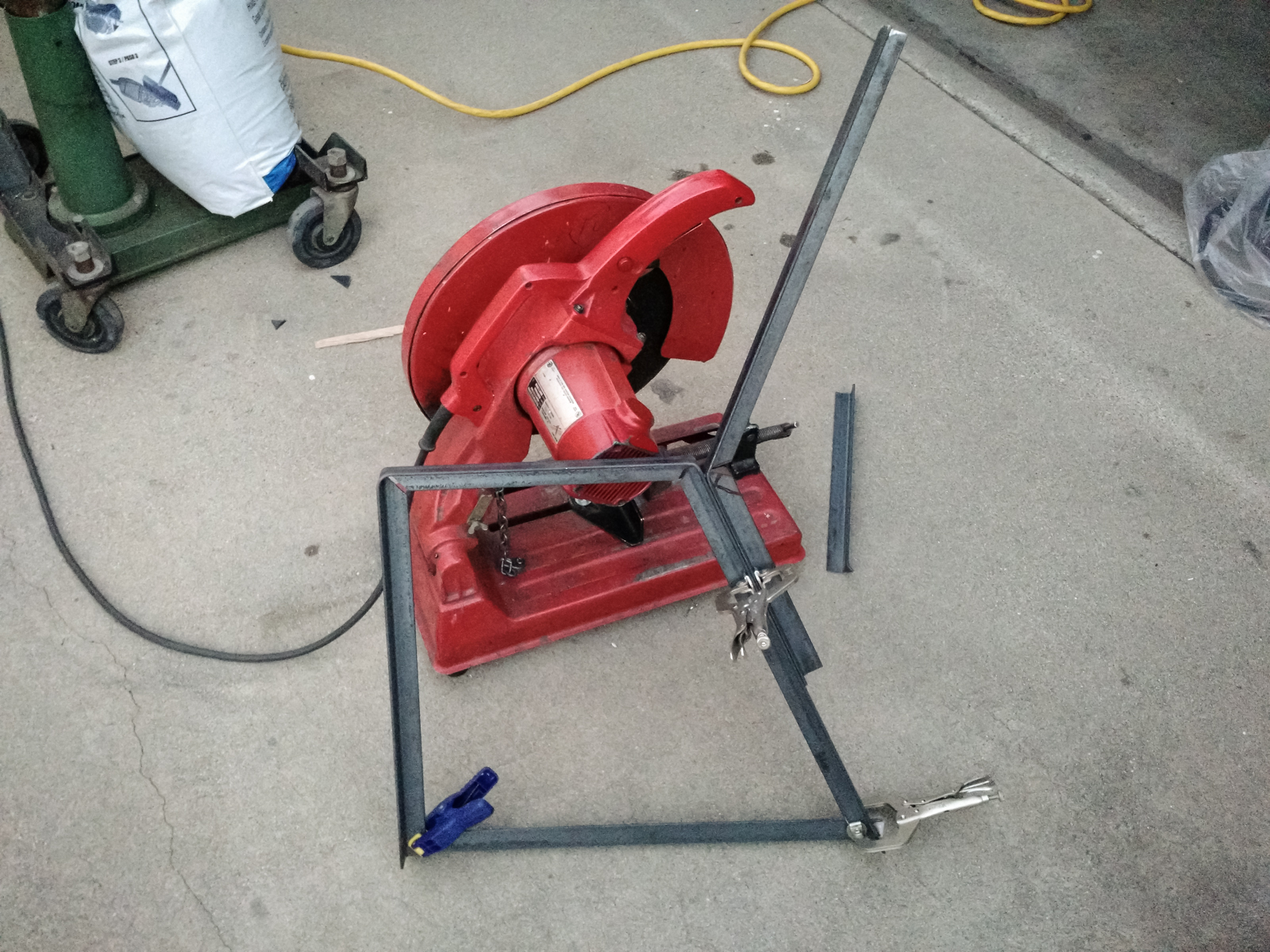
The third day of fabrication all centered around building the actual legs/ support base of the mockup and getting everything plumb, level, aligned, attached and welded. Their were some tricky corners that took some clamps and a whole lot of thinking and mark/measuring to get things to line up and work. All the thinking required a break and snack of red tangos. Once everything was welded I was anticipating the need up additional supports/ struts but to my pleasant surprise after all the welding it was quite solid and stable.

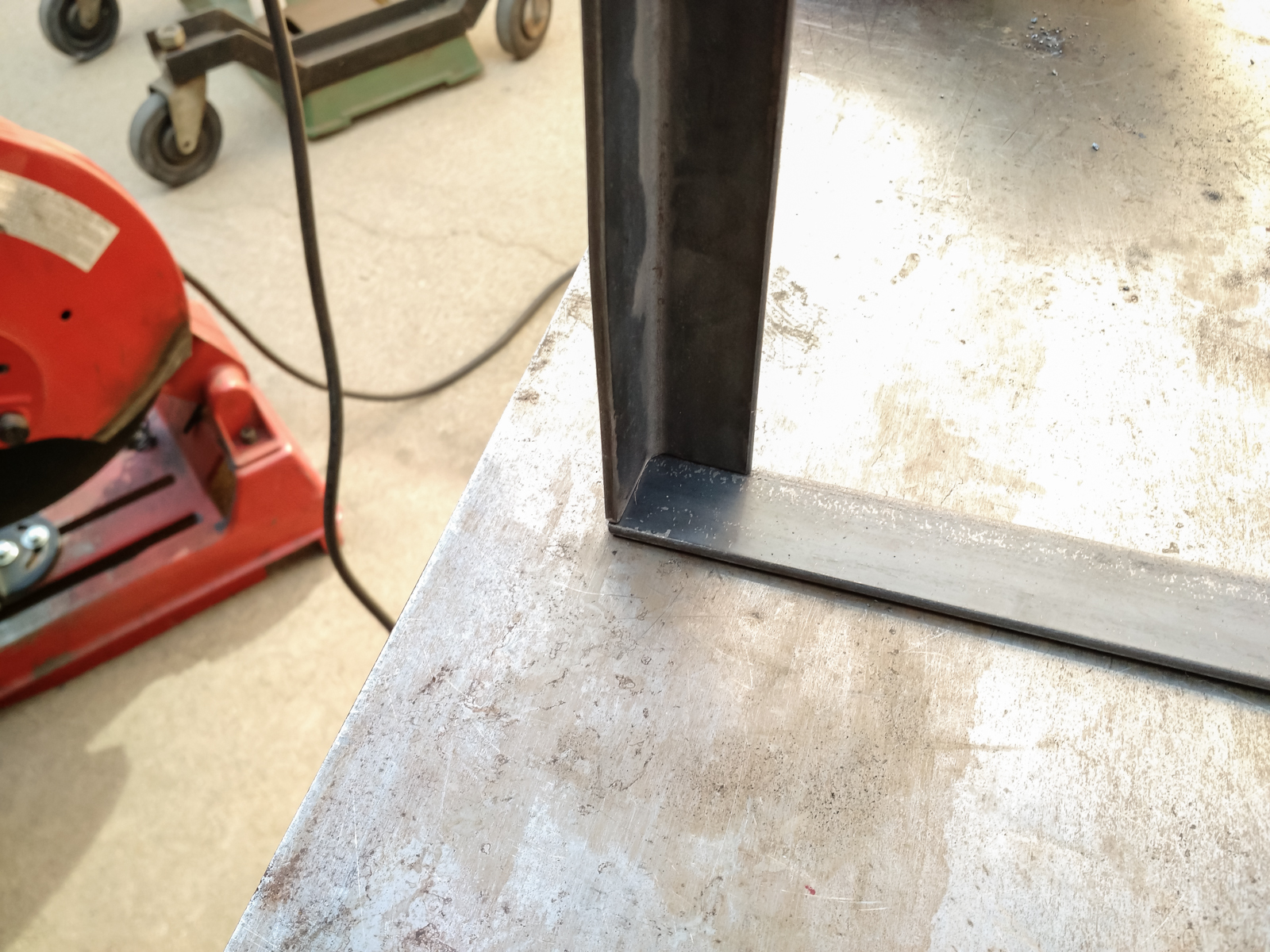


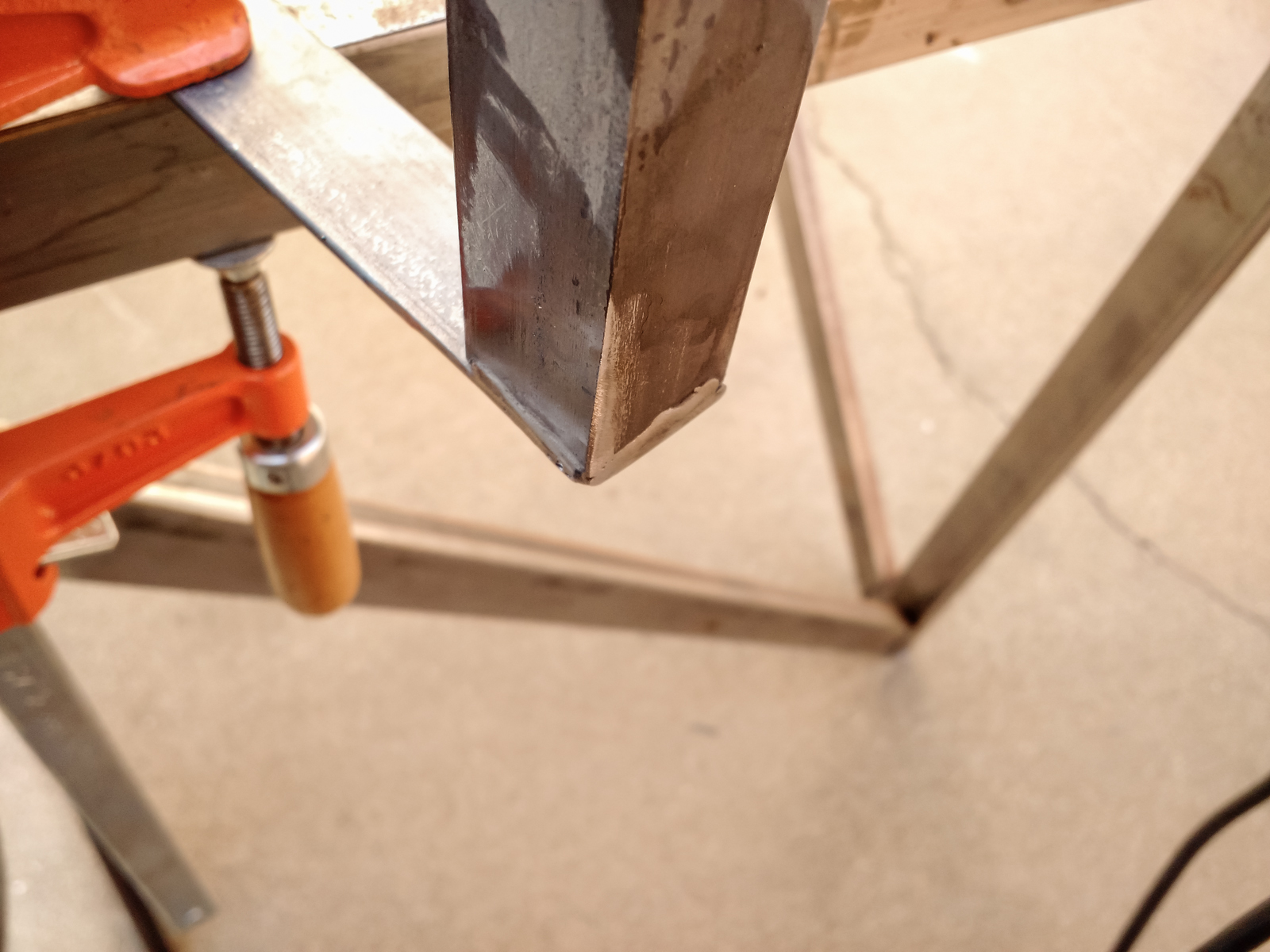
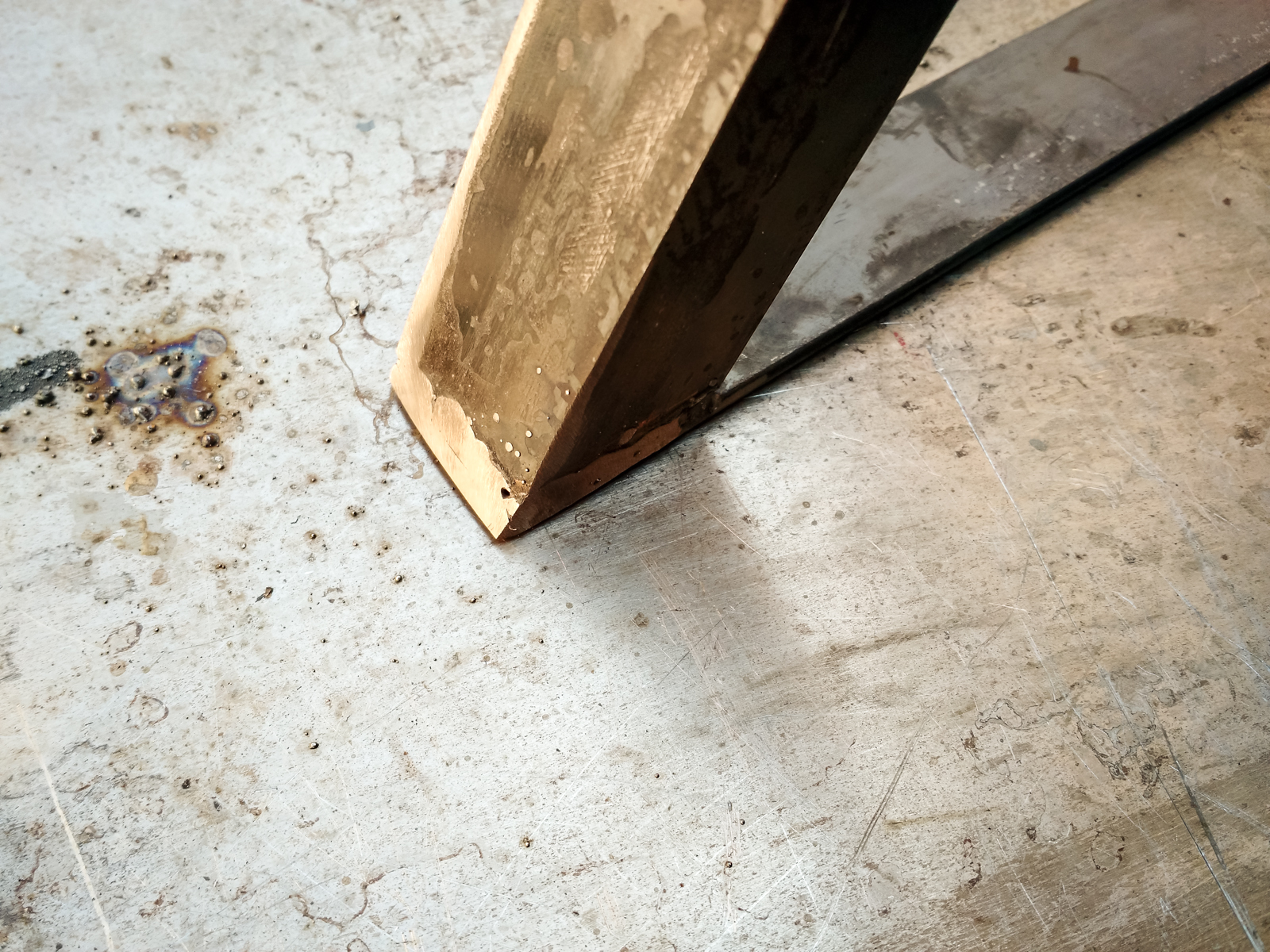
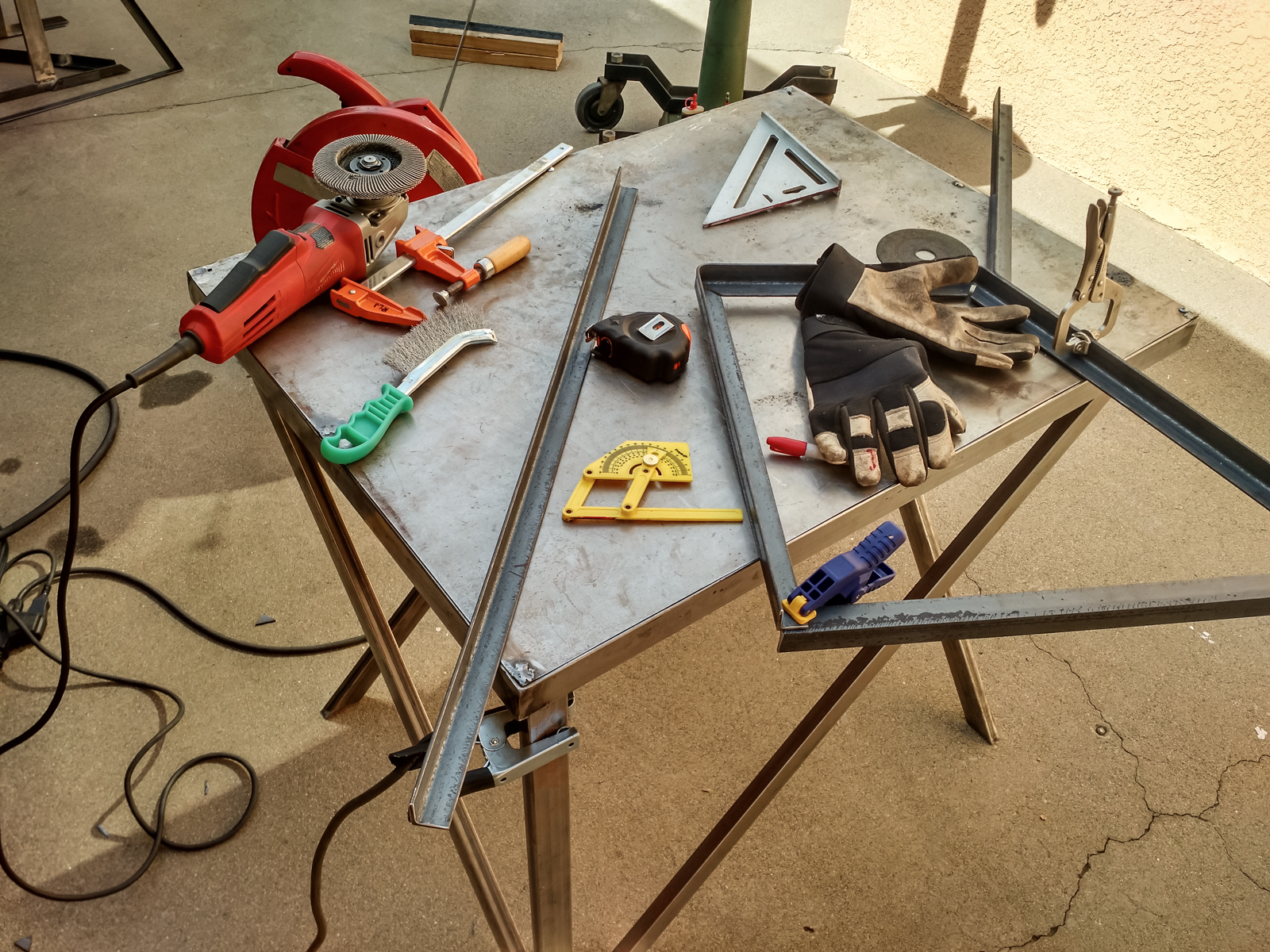




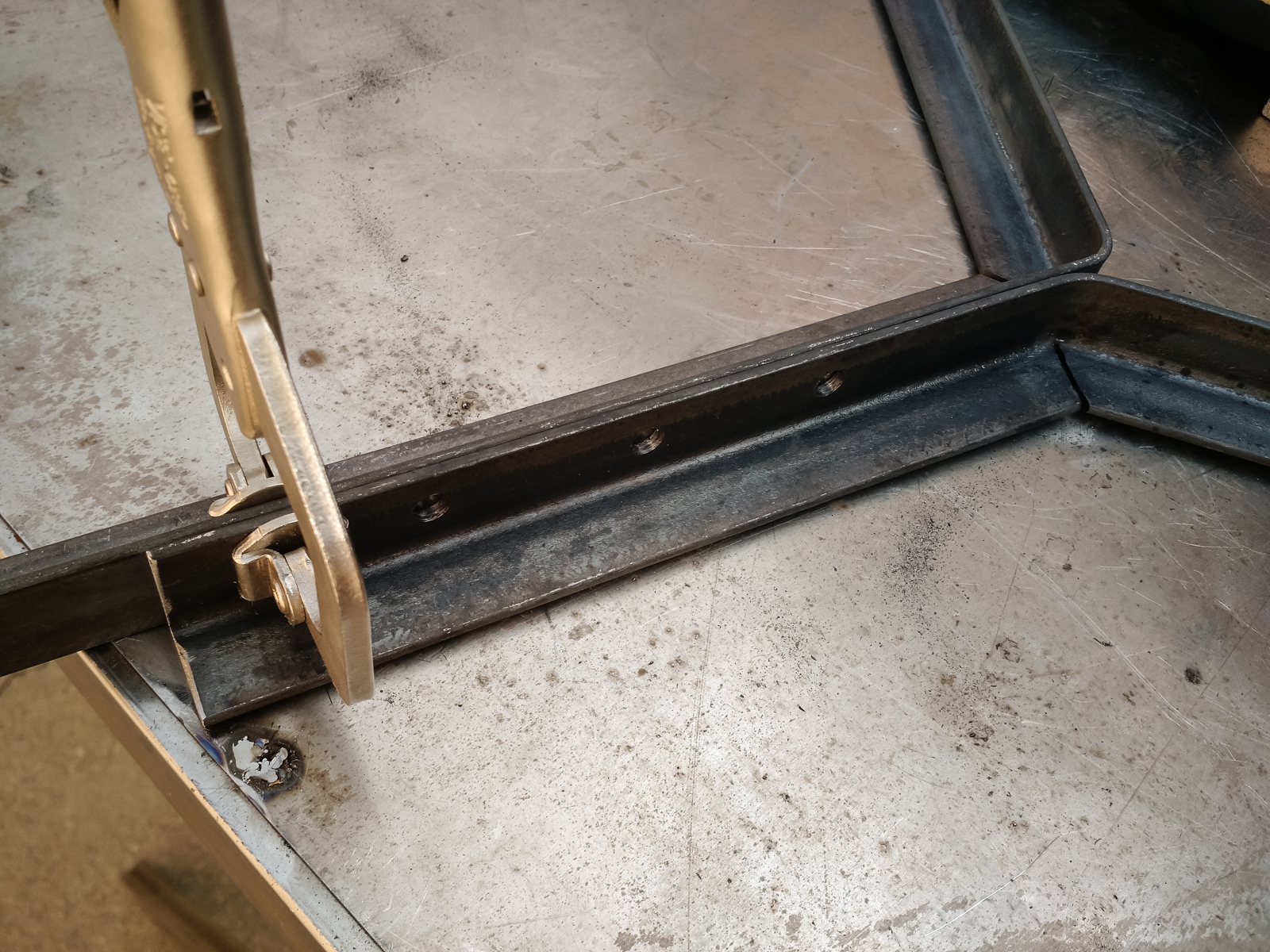

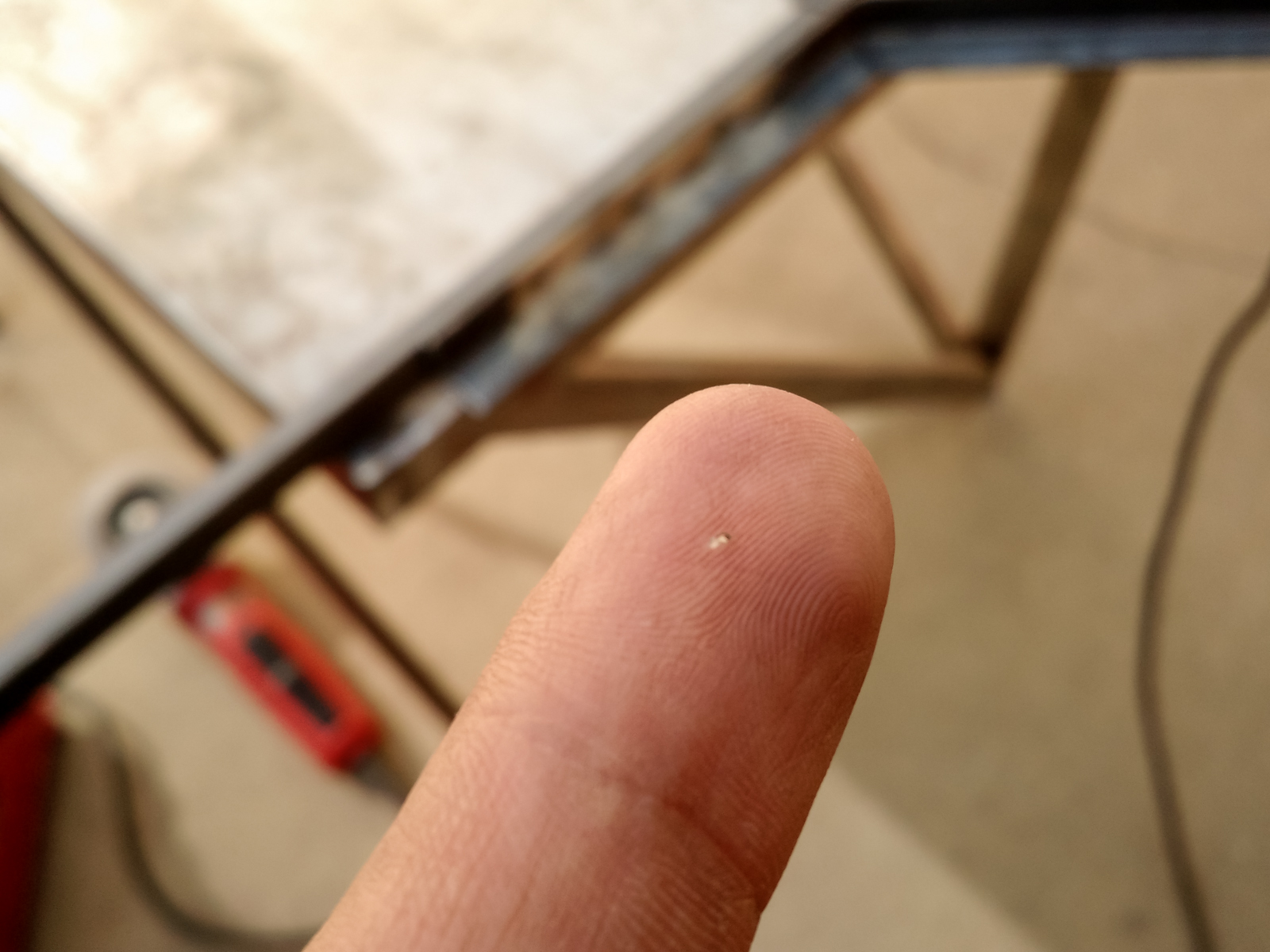






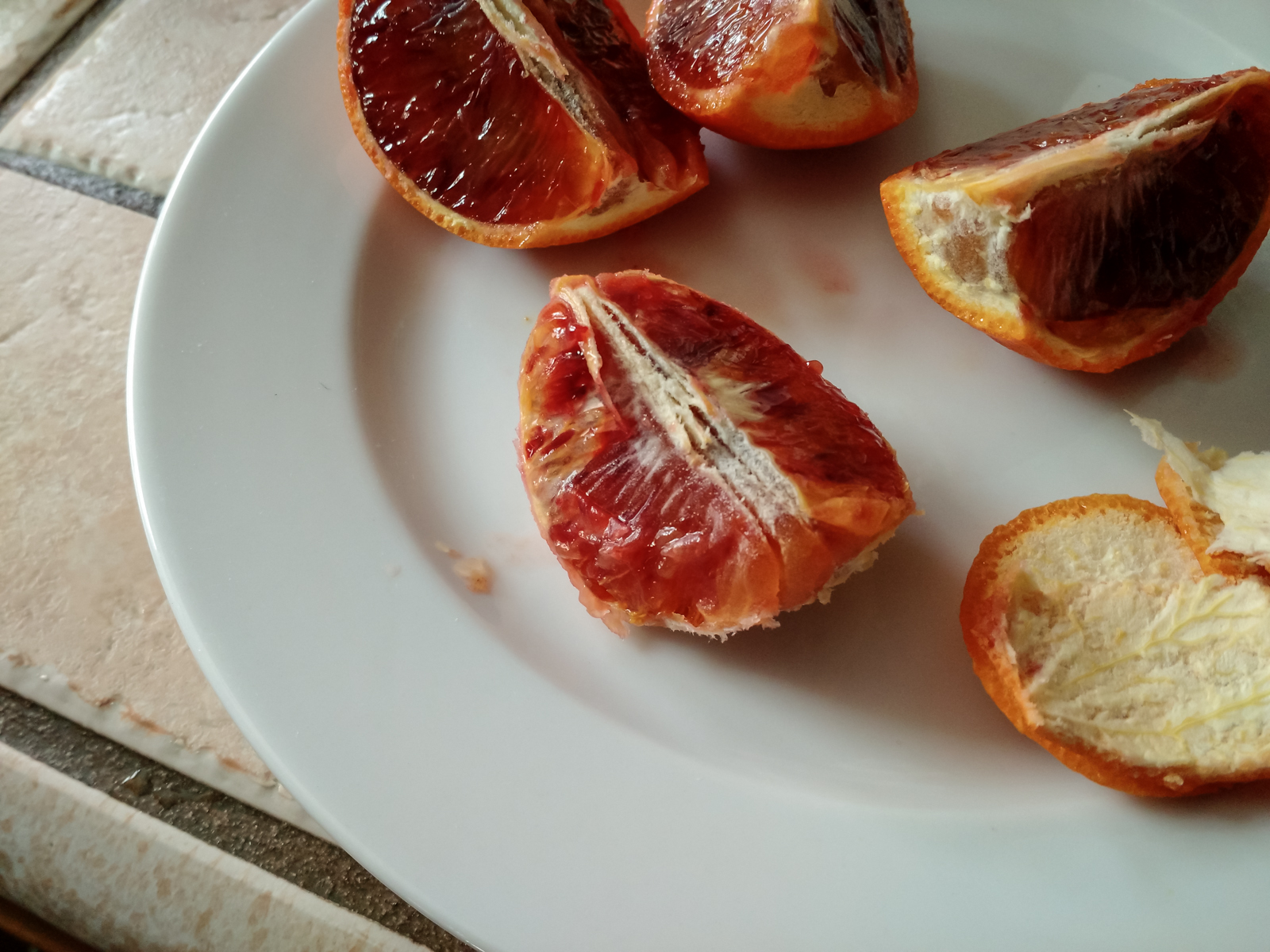
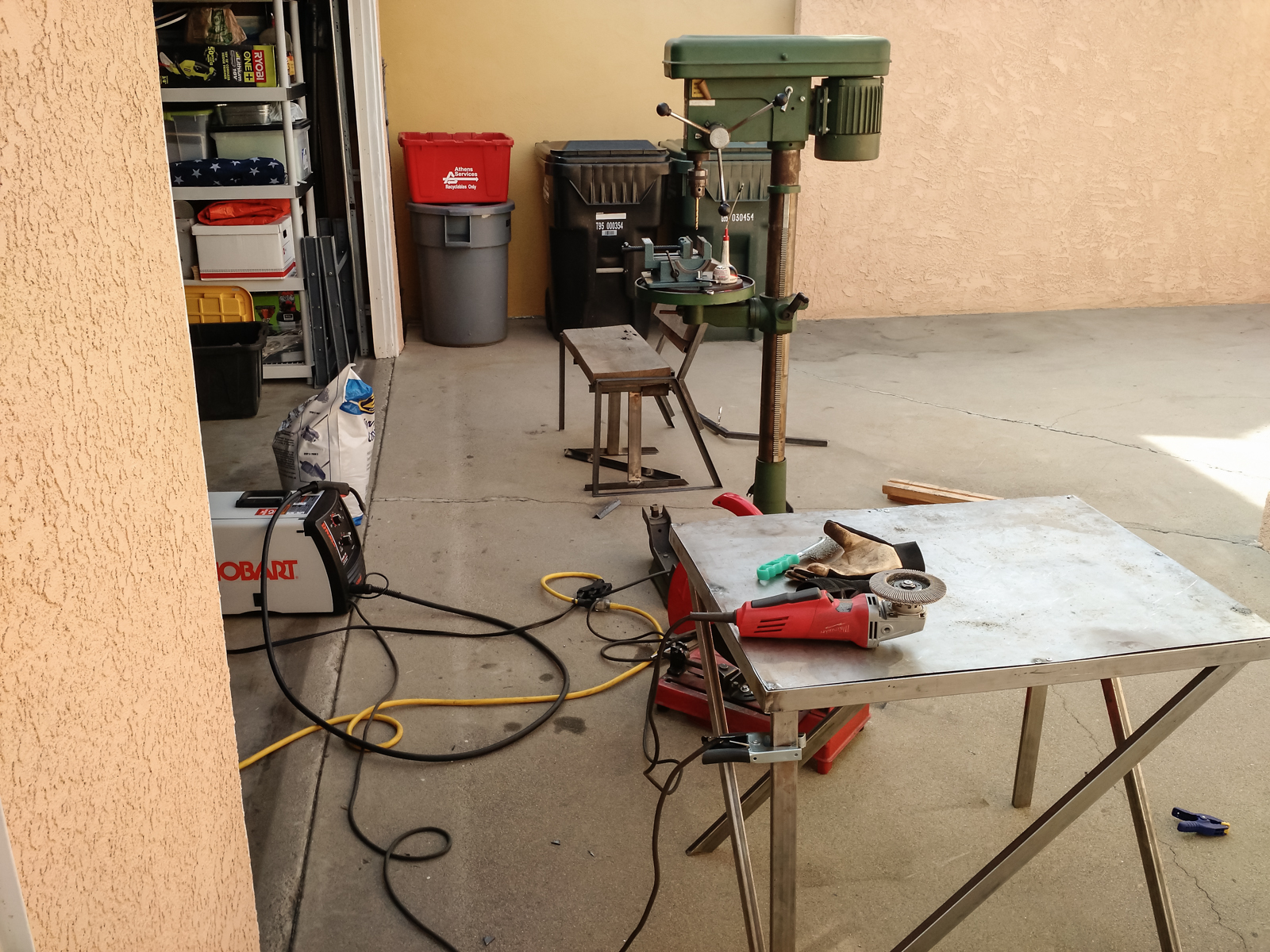

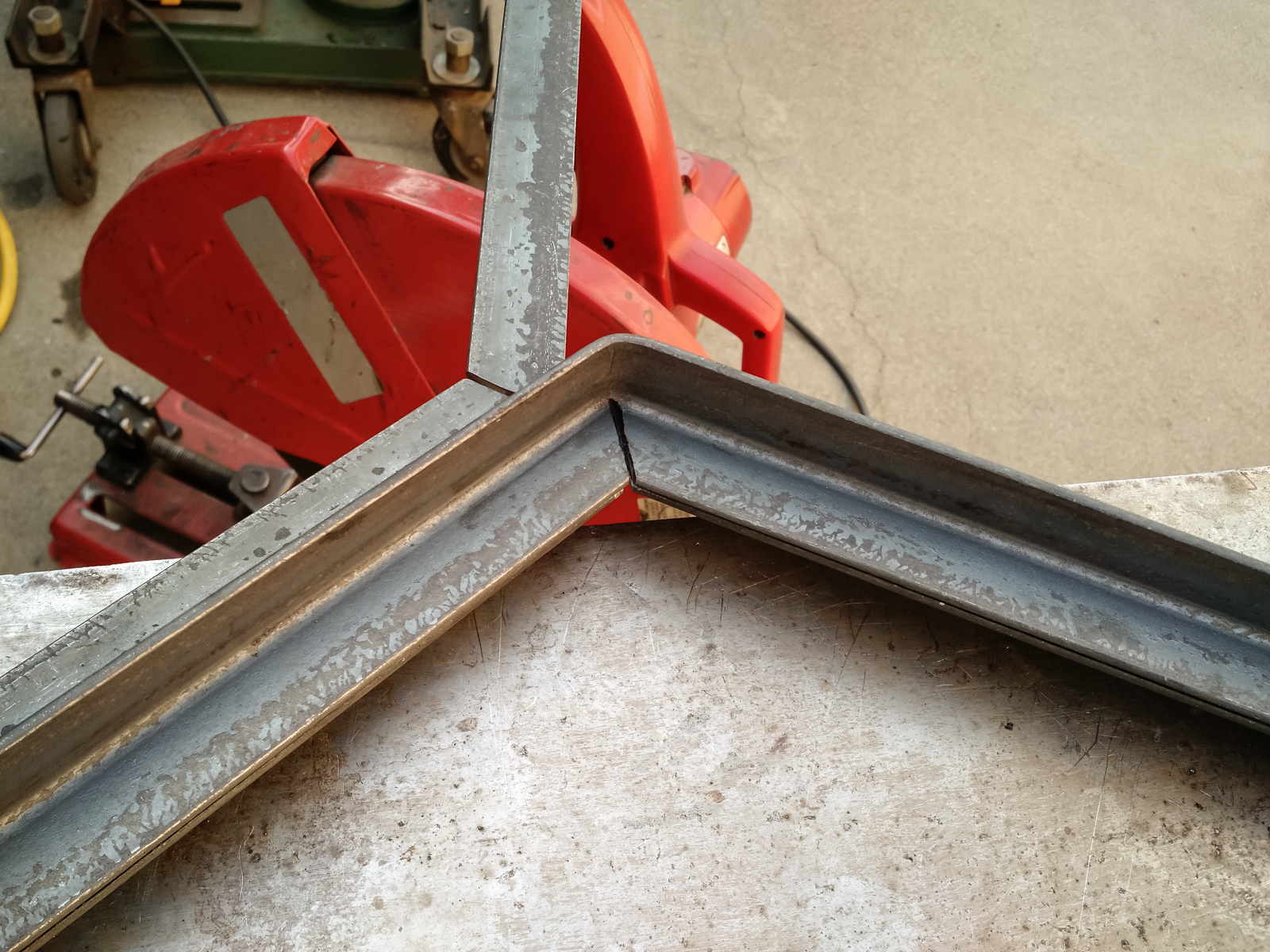







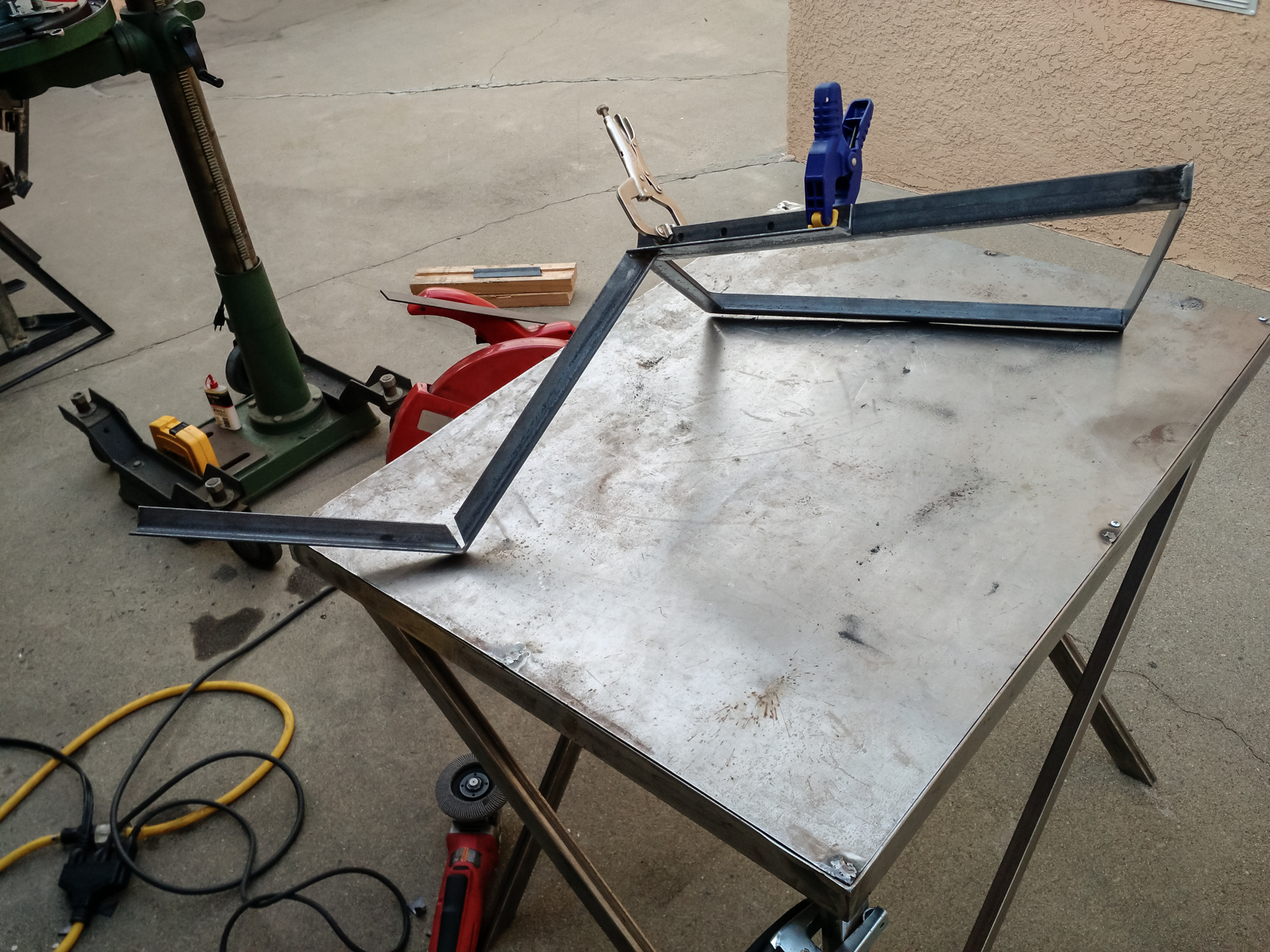


Day Four was the last day of fabrication and it consisted of finish welding, grinding, sanding and cleaning the steel and wood in preparation of finishing.
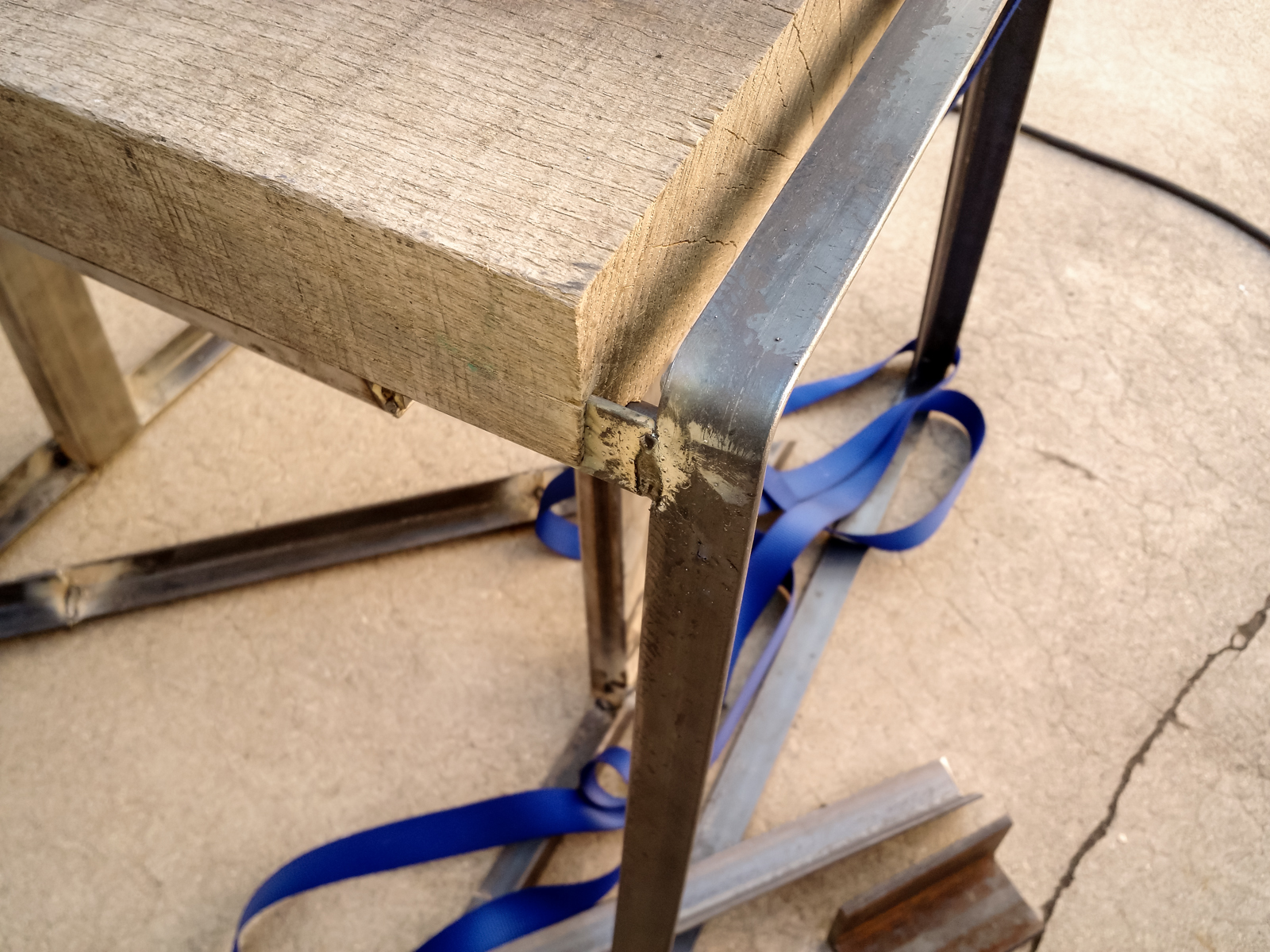

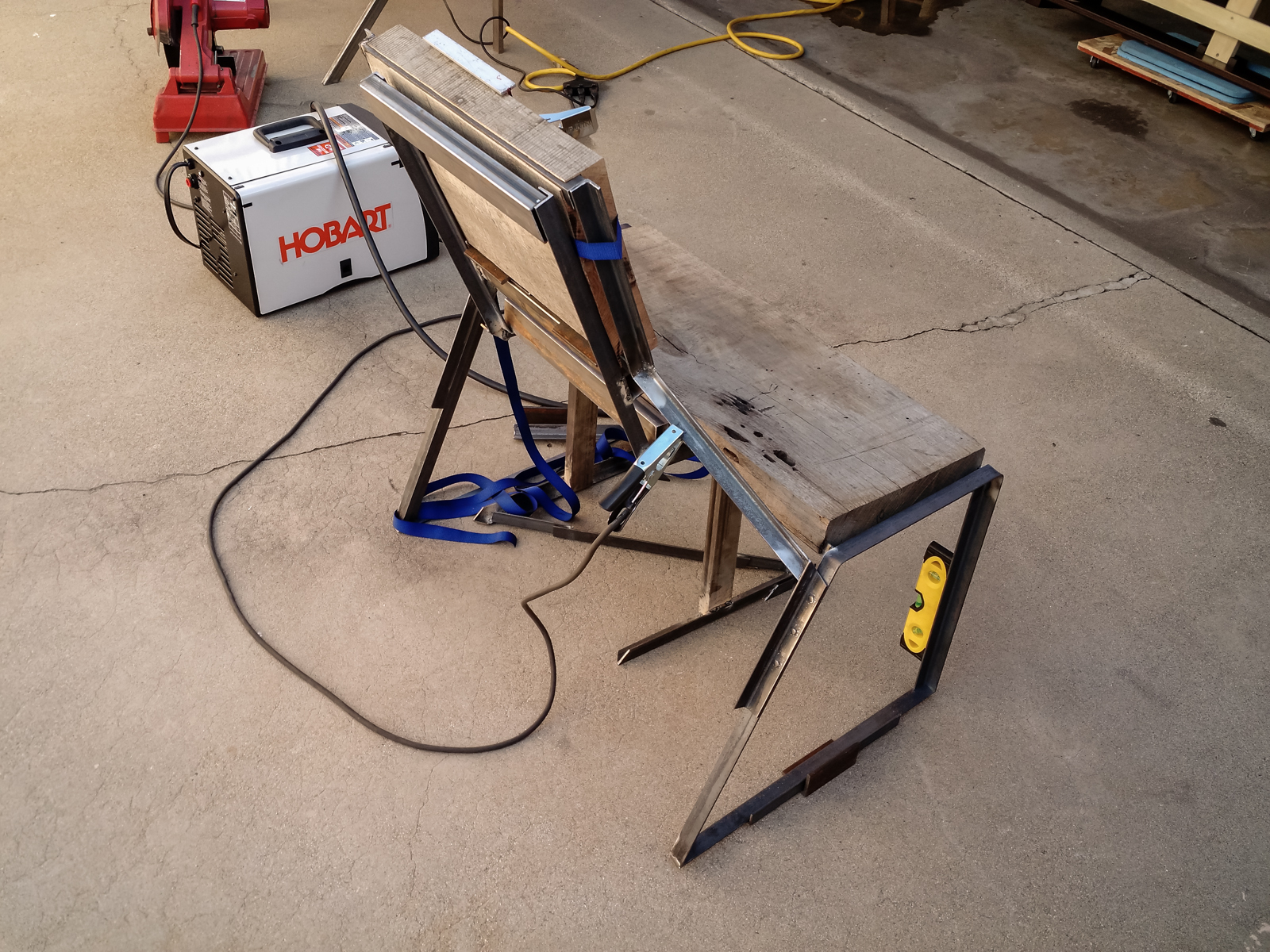

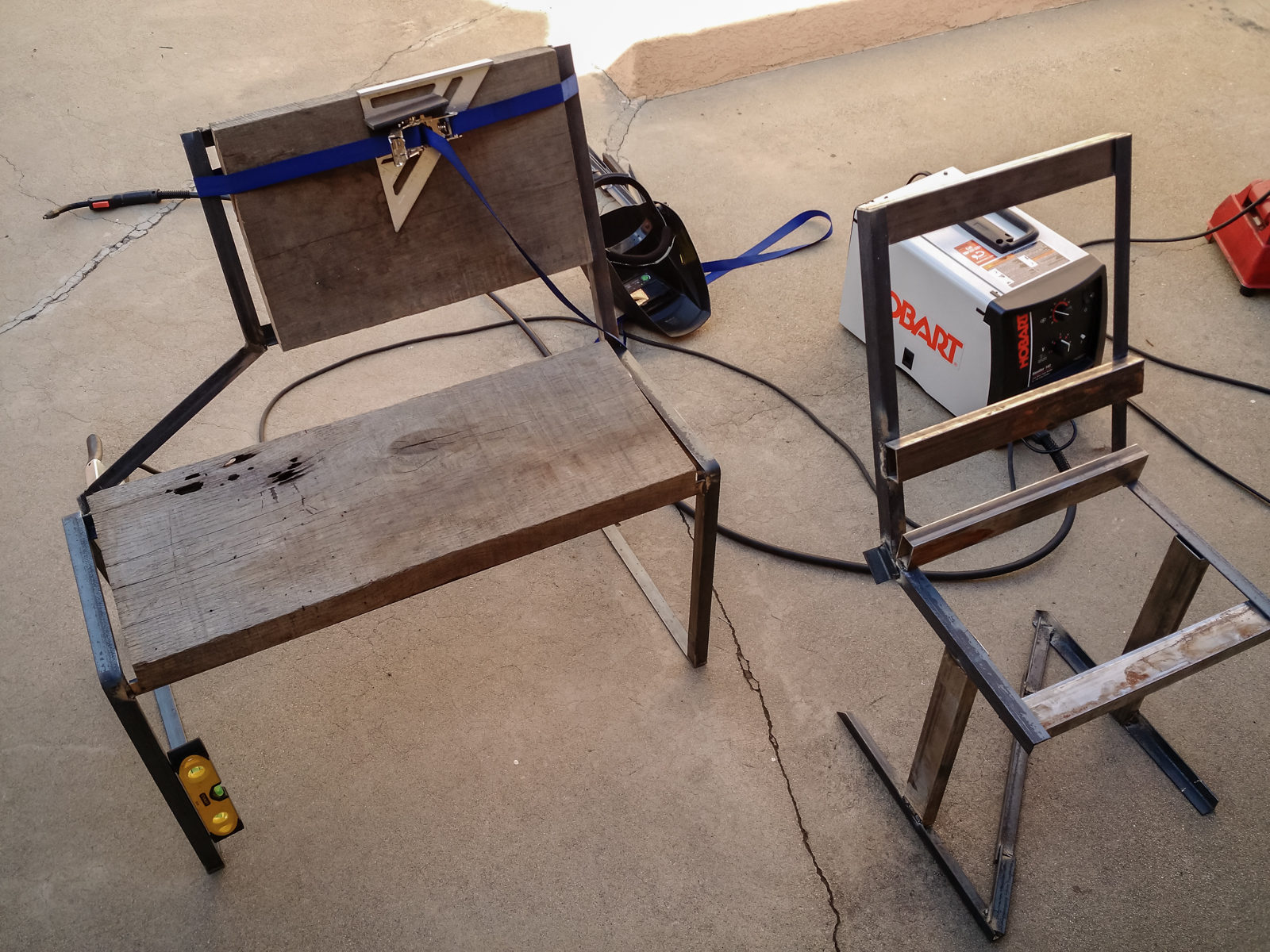




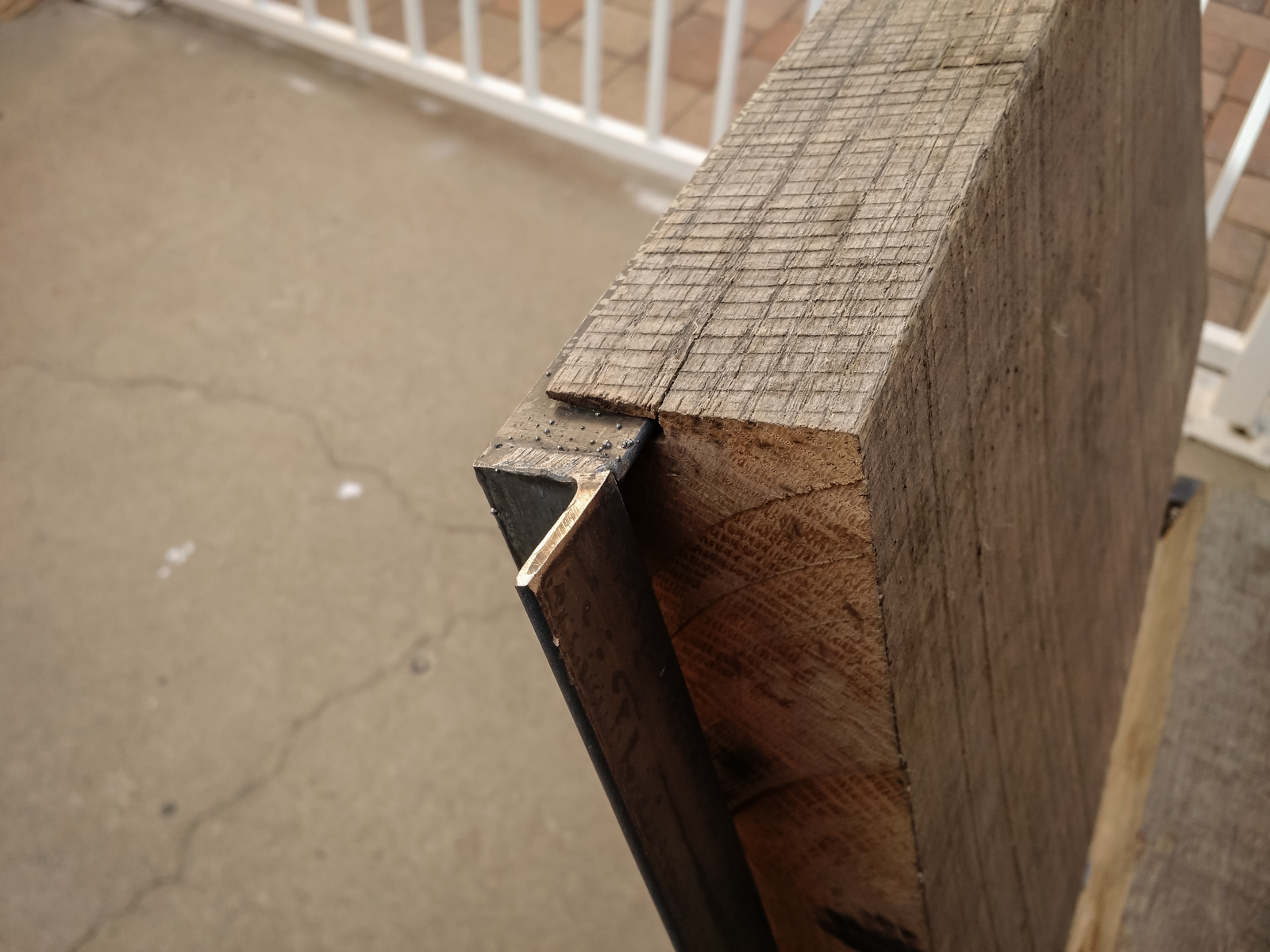



The fifth and final day was more laborious than I initially anticipated. As a result of embedding the steel into the wood and only using a pin and welding connections the wood is un-removable, hence, the finishing has to be done in one piece. This meant that for each material had to be masked and finish separately but together. I also ended up having to touch up the steel since the tape affected the finish upon removing.
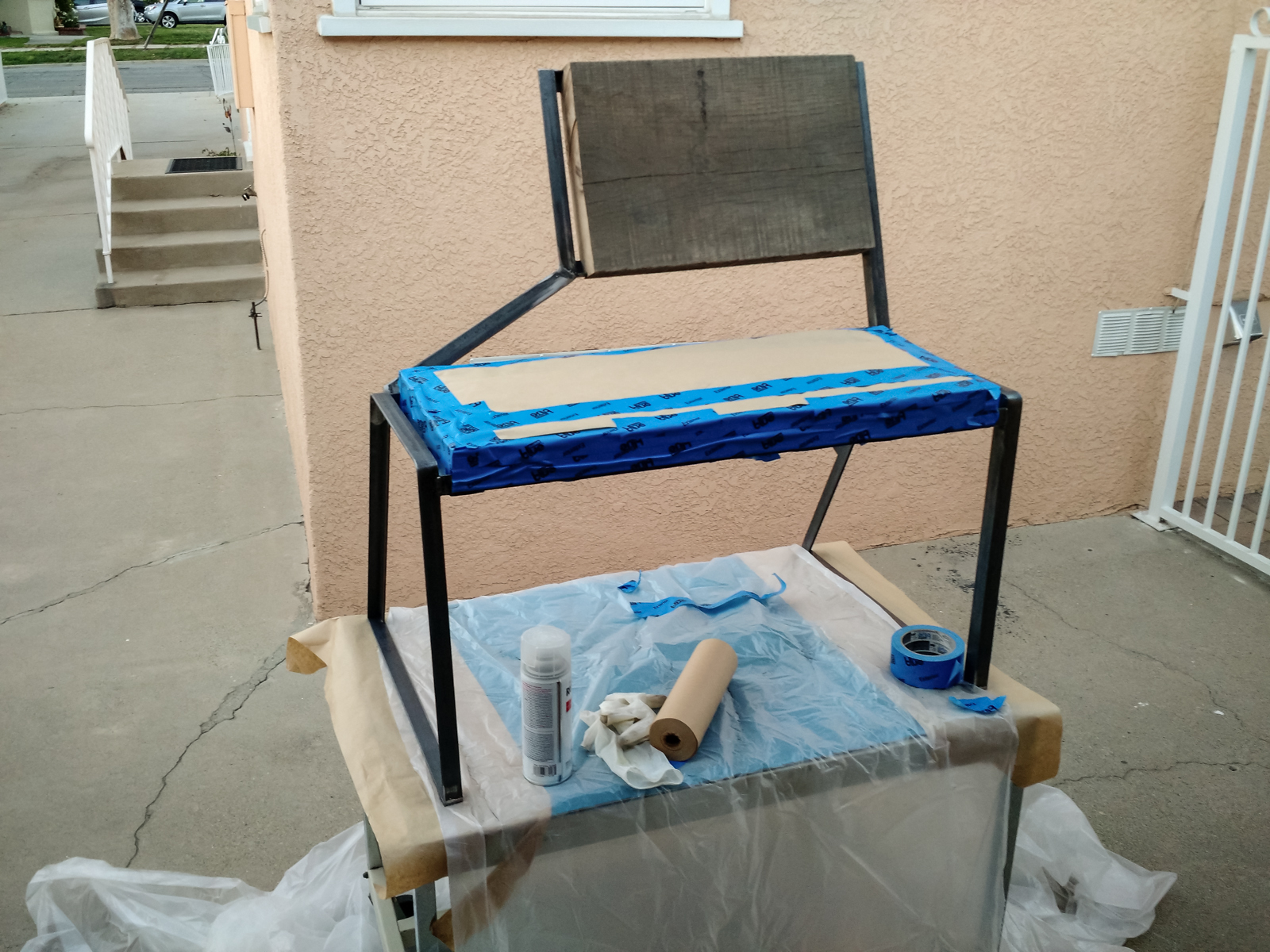
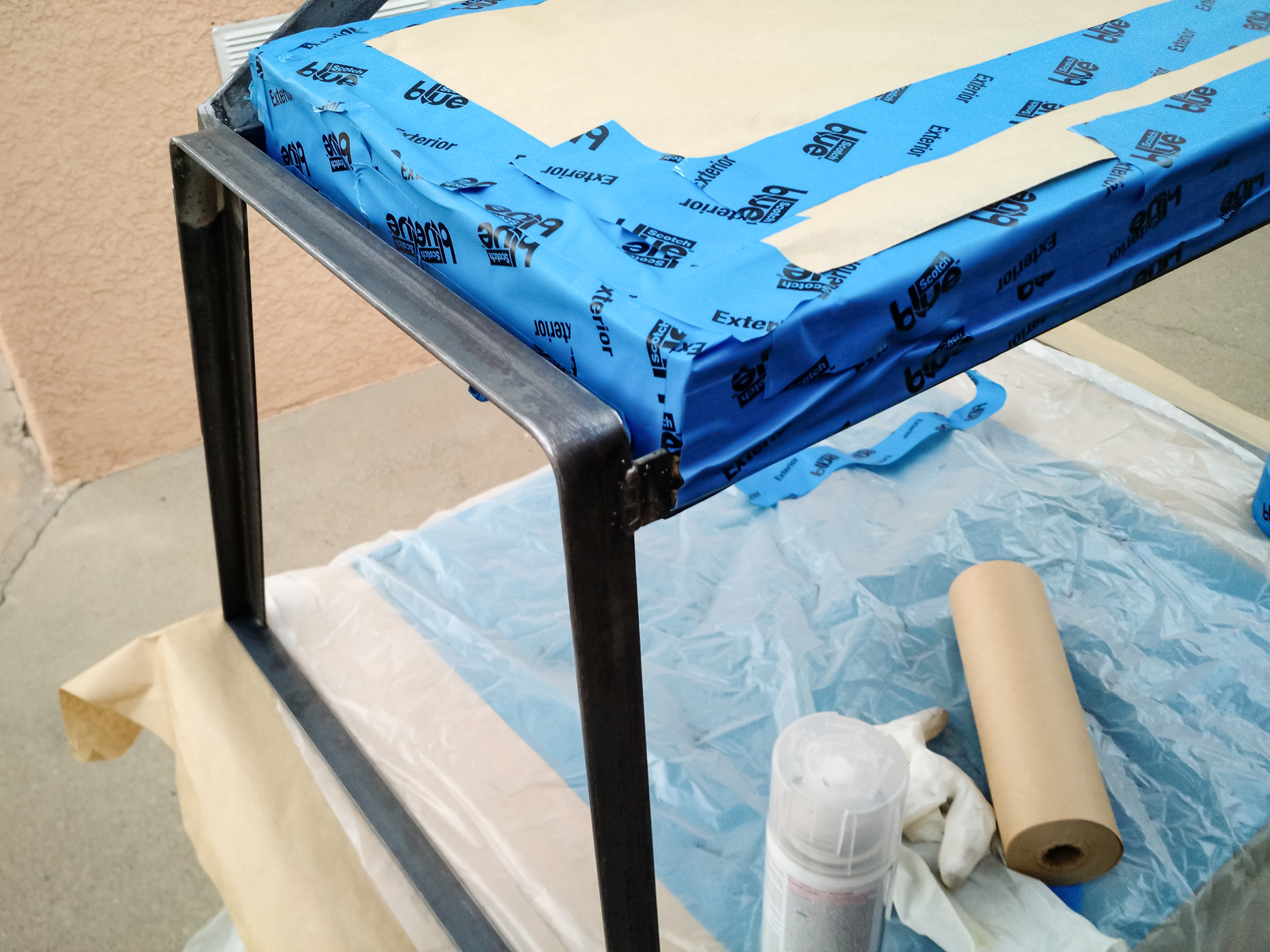



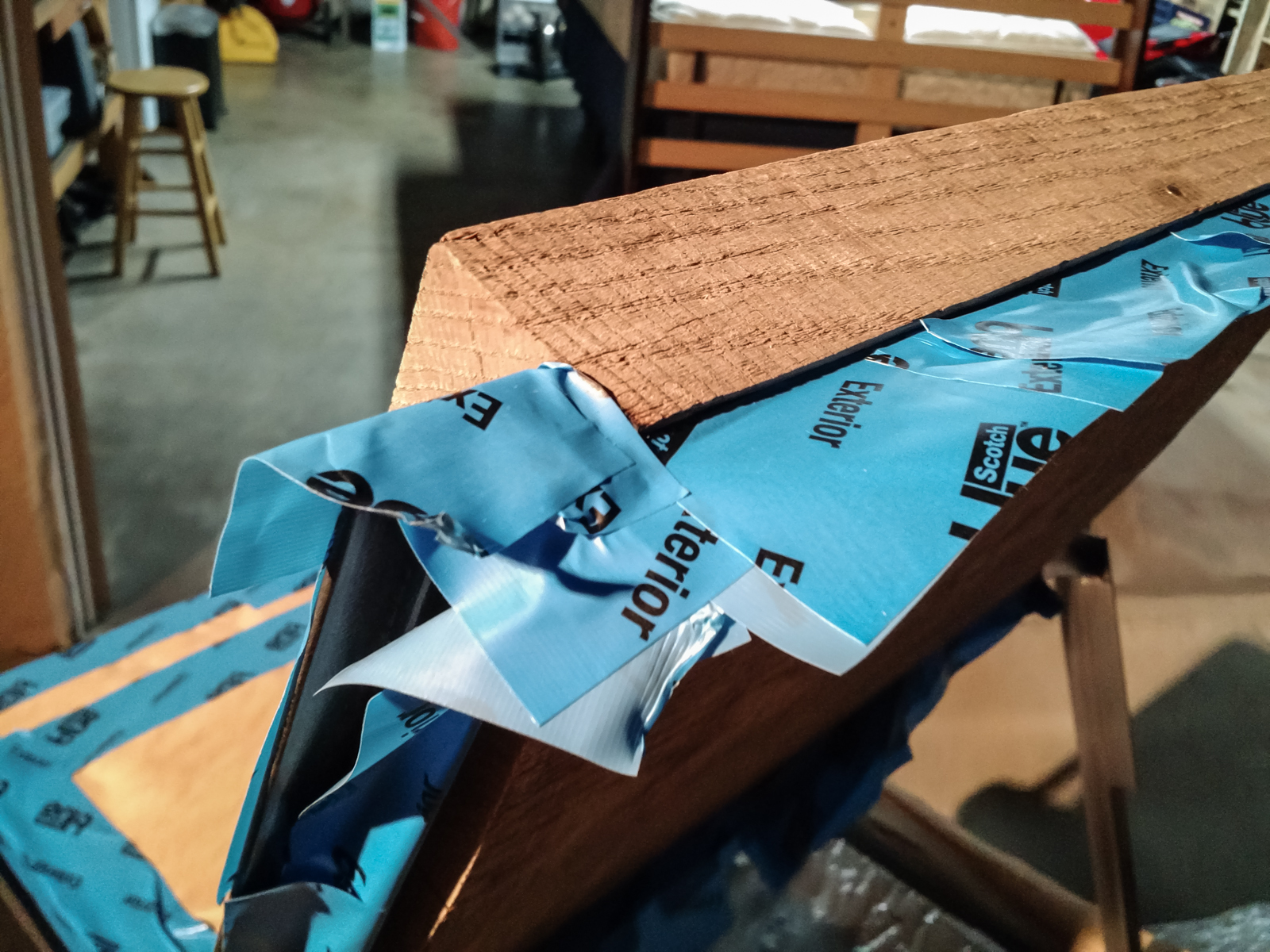

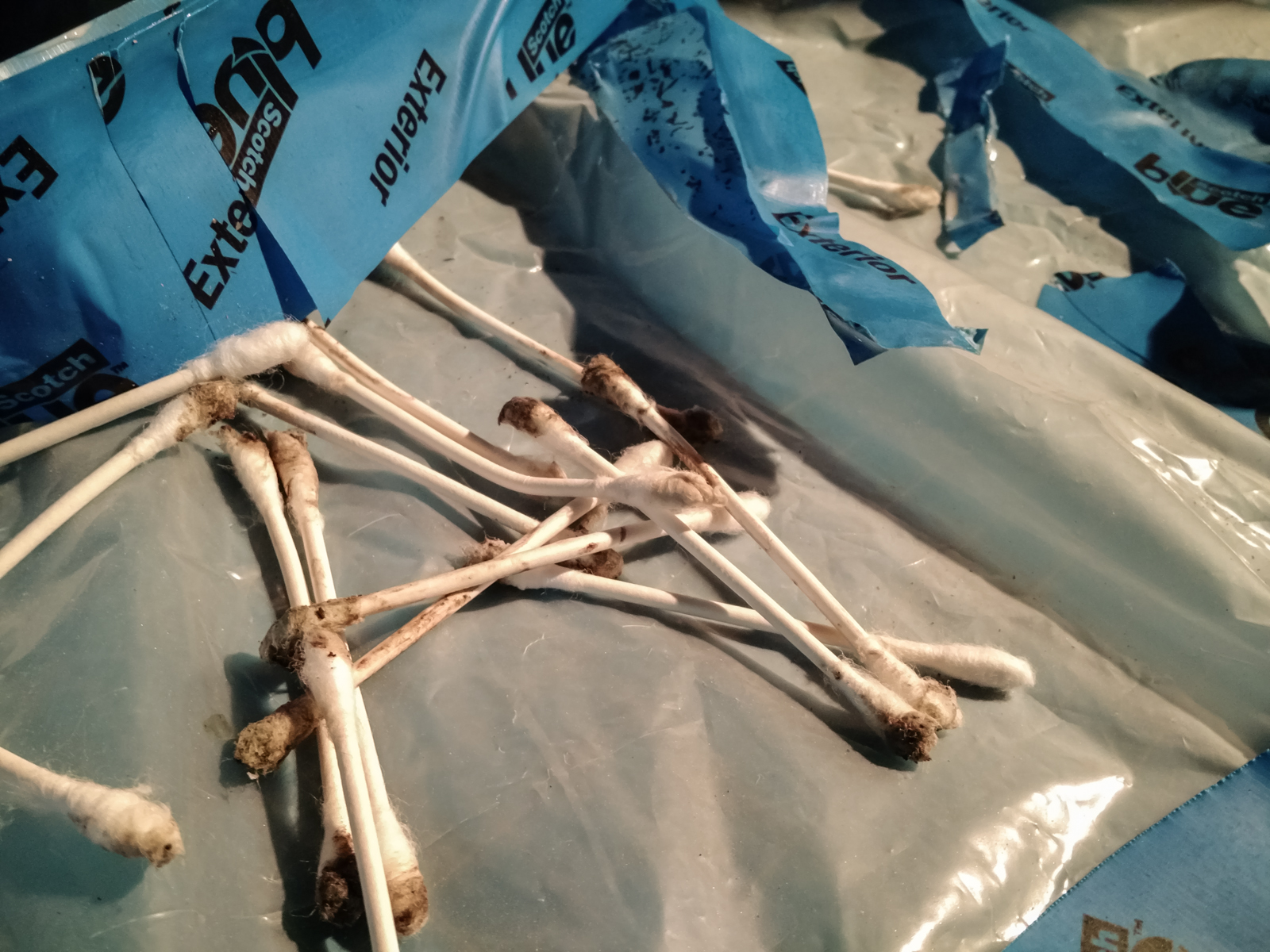



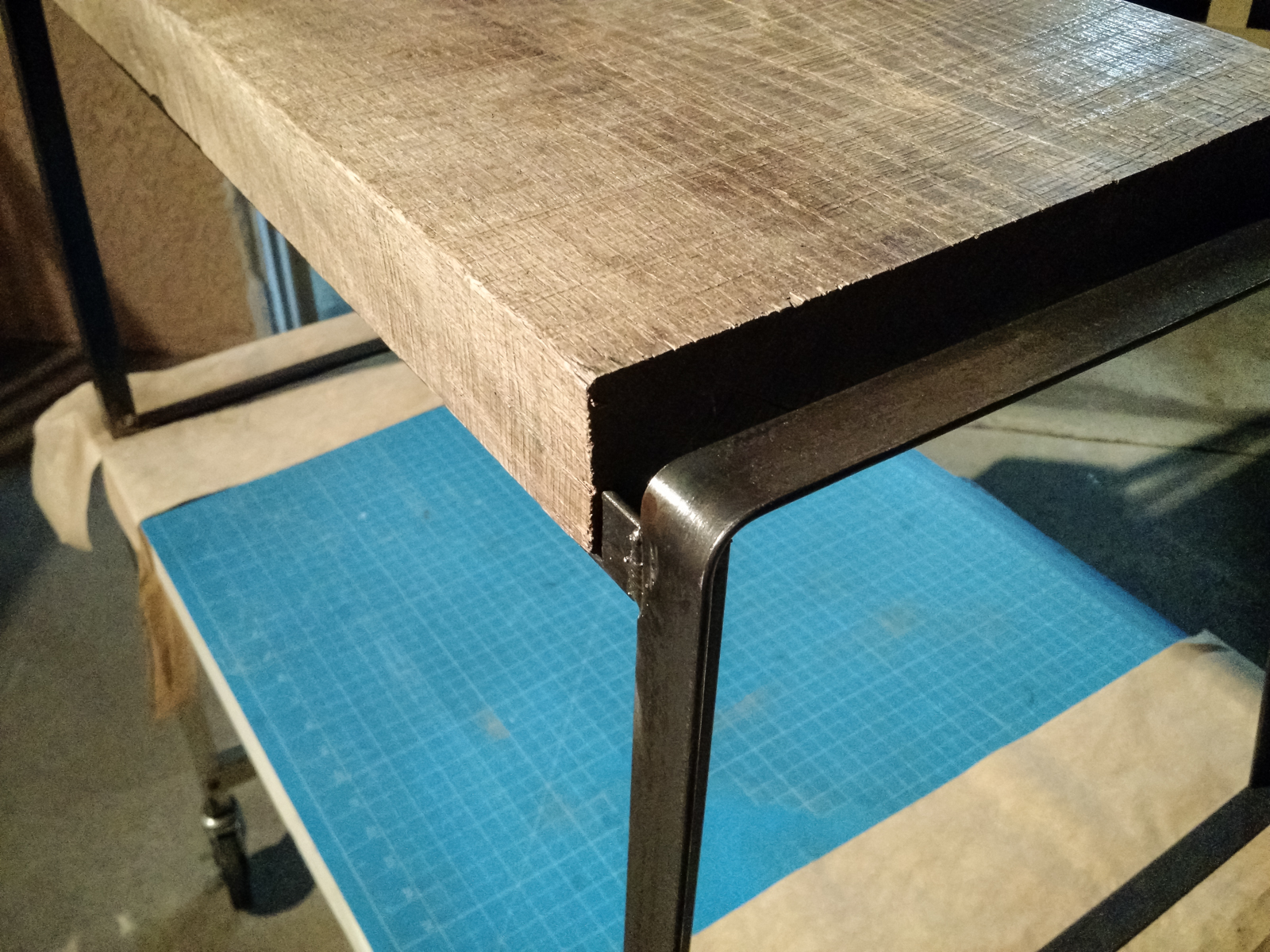


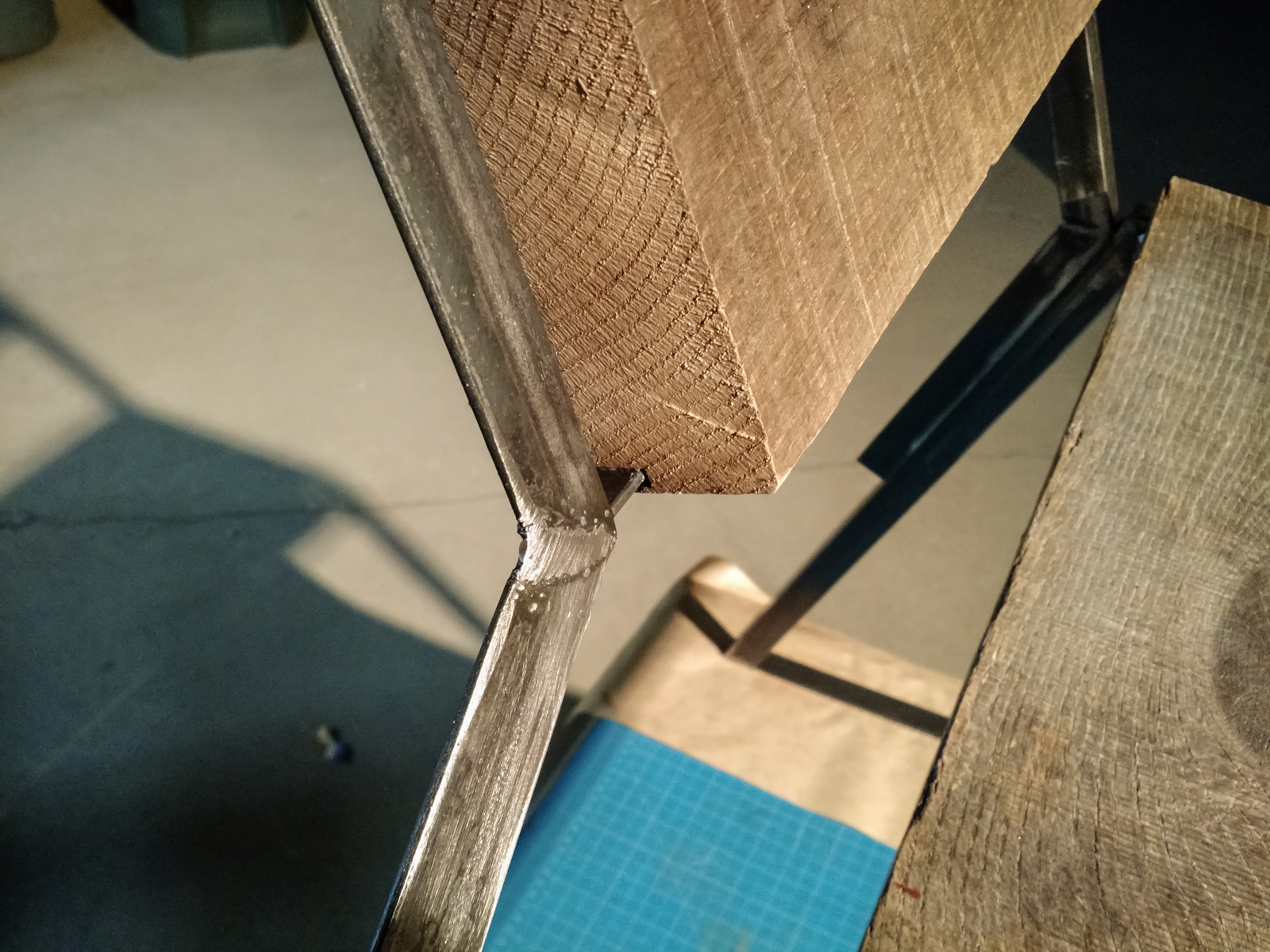